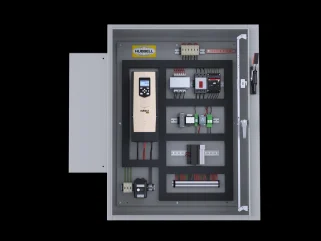
The transition from DC to AC technology marked a significant shift in industrial motor control. As AC technology emerged, manufacturers developed increasingly robust silicon-controlled rectifier (SCR) crane motor controllers, eventually progressing to modern variable frequency controls.
The middle 20th century saw the widespread adoption of SCR/Thyristor-based controls, which offered unprecedented advantages – high starting torque, stepped or infinitely variable speed control, and reduced contactor maintenance requirements. However, these systems relied on AC wound rotor motors (WRMs), which, while durable, demanded higher investment and maintenance costs compared to today’s standard inverter duty squirrel-cage motors.
Bridging the gap
Modern variable frequency drives now bridge this technological gap, offering compatibility with both types of motors and enabling a smooth transition from legacy to contemporary systems.
The industry landscape today reflects this evolutionary process, with many manufacturing facilities, highway bridges, shipyards, and government installations still operating with older SCR/WRM systems. However, the growing obsolescence of SCR control components has created challenges for maintaining legacy systems. As replacement parts become increasingly scarce, facility managers face a critical decision point: how to modernize their crane systems while maintaining operational continuity. Modern variable frequency drive systems offer a solution by controlling both standard, drive-rated induction motors or existing wound rotor and conical motors. This provides a flexible pathway to modernization, while allowing managers to strategically plan motor replacements.
Hubbell Industrial Controls has supplied mill-duty crane controls since 1897. Our EC&M™ and Euclid™ brand controls are found throughout the world, operating AC and DC cranes since before the turn of the 20th century. We have continued to evolve into the 21st, having first implemented the most rugged, AC fed SCR-based crane motor controllers; and now produce equally rugged AC variable frequency controls.
From the beginning, our DC and AC controllers were and are built to handle duty cycle extremes, extreme heat, and conductive dust. Combined with our other Hubbell brands, we offer complete electrical control and connection solutions for cranes, highway lift bridges, and mill controls.
Our rugged SCR/thyristor -based controls meet all the traditional requirements for high starting torque, stepped or infinitely variable speed control, and minimal contactor maintenance. However, these controls require AC WRMs, which are more expensive and require more maintenance than today’s standard inverter duty squirrel-cage motors. Our newest product, the VariMaxTM AC variable frequency drive (VFD), is designed to control both motor types, allowing seamless transition from old to new controls.
However older SCR/WRM systems remain in manufacturing facilities, highway bridges, shipyards, and government facilities. While there are many SCR analog drives installed in the field, the recent obsolescence of many solid-state control components has outdated this control method. With parts difficult to acquire, crane owners need another avenue to keep their existing cranes systems running.
A new approach
AC VFD systems, while used primarily with standard lower cost drive-rated induction motors, can also be used with existing wound rotor and conical motors.
Application flexibility makes VariMax drives suitable for the widest range of crane and mill control applications. The VariMax drive allows crane owners to transition to newer systems, while maintaining existing motors. This provides time for crane owners to review and determine motor replacement at leisure, while realizing the benefits of a modern drive system.
VariMax controls are designed for the same extreme conditions as our other mill-duty crane controls. VariMax drives control the speed and torque of AC induction motors in the toughest industrial and commercial applications. Built and designed for performance, energy efficiency, reliability, precise handling, and superior motor protection, VariMax VFD controls optimize crane processes while achieving significant energy savings. VariMax drives are equipped with advanced features: programmable digital inputs, built-in diagnostics, superior speed-torque performance, with internal and motor protection mechanisms that enhance functionality and system durability.
Why move to VFDs
The rise of SCR controls systems in the industry was spurred by the movement away from DC power to AC power. AC systems required wound rotor motors because the torque and speed characteristics can be infinitely adjusted, either by changing the external AC input voltage, or by changing resistance to the slip ring connections. The WR motor’s characteristics provided high starting torque, ideal for hoists, mills, conveyor belts, pumps, and movable bridge applications. In addition, the speed control of these motors ensured smooth operation under variable load conditions, ideal for crane hoists where load can change each lift. SCR controls provided good control of the hoist load conditions: full loads, overhauling loads, and empty hook loads. However, with the rise of the digital era, SCR analog drives, while robust, were overtaken by the more efficient, more communicative, and increasingly more flexible variable frequency drives.
Existing SCR solid state AC adjustable speed motor controls provided torque limiting or tachometer speed regulated control for wound rotor motors. Performance was achieved either by adjusting the applied motor primary voltage with primary SCR bridges, or by control of the WRMs secondary impedance via secondary SCR bridges; or both. SCR control units consist of regulator and firing circuit boards, adjusting the SCR bridge conduction period in response to changing demand, adjusted via motor feedback from a torque or speed reference signal. SCR controls were typically available either with two to five speed points (stepped control) or were adapted to infinitely variable control inputs. Operator inputs to the controls system provided creep speeds, full speed and reduced torque when needed. Variable speed inputs were often provided via master switch mounted stepless inductor units; or master switch- or pendant- mounted potentiometers.
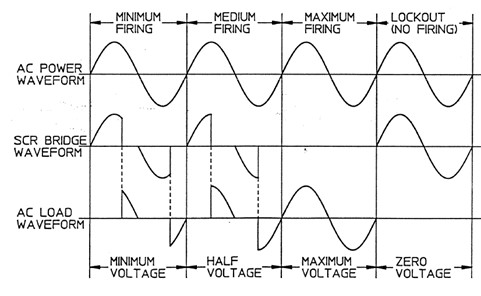
Fig 1: SCR Power Control method: Primary Voltage Control
Reference Figure 1. SCRs for primary motor controls operate to control the firing angle of the silicon-controlled rectifiers, providing an infinitely adjustable voltage to the WR motor primary. Unfortunately, SCRs cannot be turned off once gated on, requiring natural commutation to turn off. This meant a separate isolation contactor was required to interrupt motor power.
By contrast, variable frequency drives typically use IGBTs (insulated-gate bipolar transistors), a fast-switching device that can be turned off at any time and is fast enough to generate a pulse width modulated (PWM) power output (See Figure 2). The transistors switch a DC voltage on and off with a defined sequence, with time on and off adjusted to most closely replicate the AC motor voltage and current, with output adjustable to any frequency. The change in frequency applied allows induction motors to maximize the output torque produced.
However, pulse width modulation and fast switching causes electrical noise on motor windings. As a result, windings on inverter duty motors have Class F or higher insulation rating, complete with insulation systems specifically made for use with VFD drives. Inverter-duty motor insulation systems are rated 2000 – 2200 V, compared to 1600 V in a standard motor. Higher rated insulation systems help protect motor windings from damage over time from the PWM. However, most wound rotor motors predate modern insulation systems, and have only resin-loaded tape, with the slip rings directly connected to the brushes. This risks damage to the windings and the slip rings via electrical noise generated by VFDs. To combat the noise problem using VFDs, a dV/dT filter is added to the drive output to protect older existing motor windings. The filter slows the rise rate of voltage transient increase and minimizes the peak transient voltage. The filters also reduce the reflective wave that can exist on long motor leads, should the leads be long enough for the reflection to match the time for the transmission of the standing wave on the circuit. The dV/dT filters help protect WRM windings from overheating, as well as protecting the drive from any voltage being reflected.
Another advantage to VFD controls is the removal of any external WRM secondary resistance. The resistor sets are no longer needed, as they were for SCR systems. In SCR systems, the external resistors were needed to improve speed-torque performance. VariMax variable frequency drives do not need WRM slip resistance; and these are removed. The WRM secondary windings are connected, either by internally welding the secondary windings (best practice, as it removes motor brush maintenance, and best emulates a standard AC induction motor) or by connecting the 3 secondary lead wires outside the motor. Note that if the secondary lead wires from the slip rings are shorted, the slip ring brushes will still need service at regular intervals. As mentioned, shorting the rotor windings on the motor allows performance more like a standard squirrel cage motor, and allows variable frequency drives to maximize starting torque.
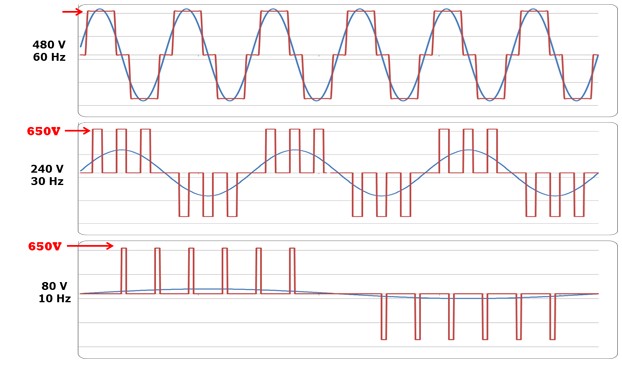
Figure 2: Pulse Width Modulation
Drop-in replacement
A challenge for the replacement of older systems and a major pain point for most cranes, is that space on a crane is limited. Replacement systems need to fit into existing space. Our systems can be built with customized back pans and / or custom enclosures to fit each crane. This allows the creation of drop-in replacements into existing space. Simple physical replacement allows for less down time during installation. Another challenge is crane wiring that has been in place for years, if not decades, can be difficult to reroute due to location and age. VariMax systems allow existing wiring to operator controls via joystick, radio, or chair to be adapted for use with new controllers. VariMax can use existing five speed contacts or be configured to use existing potentiometer controls. Operators who are comfortable with existing controls will be comfortable with the change, as VariMax systems allow for more speed and load adjustment than an SCR system. VariMax can typically emulate or, if allowed, exceed the performance and speed control of older SCR systems.
VariMax control systems are designed for longevity and reliability. One enhancement: we use common and readily available 120VAC interposing control relays to send all control, limit, and brake commands. These relays are connected though standard 120 Vac control wire. Relays increase system reliability and reduce maintenance costs by providing full electrical isolation. Since our relays are common and typically found locally, on-hand spares inventory is reduced. Our systems do not use proprietary interposing ‘relay’ cards, as these do not increase anything but “spares” costs.
VariMax systems include a standard brake relay which allows connection to any existing brake system. VariMax is adaptable for use with existing rectifier-operated DC brakes, DC or AC motor-mounted disc brakes, or AC thruster brakes.
Also needed for each VFD motor system is a smaller dynamic braking (DB) resistor for each drive. DB resistors only consume power when the motor is lowering or decelerating, not while accelerating or hoisting. An advantage over other drive systems, our dynamic braking (DB) output module is built into each drive, which simplifies system connections and replacement. Just two wires are needed from the drive to the DB resistor. If the horsepower / kW is small, the DB resistors can be mounted on top or next to the VFD enclosure to minimize space.
VariMax system designs focus on convenient, quick replacement with few changes to other crane components. However, these advanced systems also have many upgraded safety protocols compared to existing SCR control systems. Among them:
- Direct torque control, with brake and motor torque proving, tests the motor before releasing the brake. This function ensures the motor provides enough torque to hold the load in place without motion. The torque proving safety feature is ideal for hoisting systems with overhauling loads. The settings help to ensure loads do not drop when starting up or upon initial operation.
- Brake slip detection keeps the system on for a few seconds after the stop signal. If any undesired motor rotation is sensed, the drive assumes the brake is no longer able to hold the load. The drive will hold the motor and load in place, and send out a fault that alarms, but does not turn off the system.
- Limit switches can be programed for direction, and slowdown or stop, and can be programmed to let the motion back out of the limit at a set speed, maintaining production without need to re-start the drive each time.
- Safe torque off and stall protection are also standard with these units.
Most of these safety related features are or could not be on SCR systems, due to their analog nature, and less precise control.
We offer several system set up options for VariMax: via a keypad located on the unit, via computer, or with a Bluetooth® connection from a mobile phone. The Bluetooth connection allows for tuning on the ground or at the operator console, to fine tune and more easily match operator preferences from a distance.
A VariMax VFD system offers many performance enhancements compared to older SCR controllers. Our ability to increase safety protocols, reduce maintenance, adapt to each installation, and adjust easily to operator preferences, makes the decision to change to VariMax drives an easy choice.