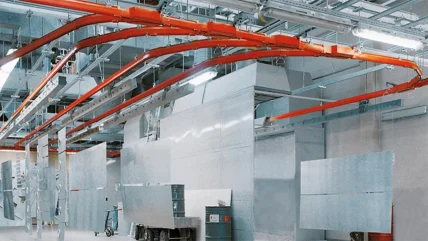
In North America, overhead lifting dates back pre-1850 when the first patent for an overhead traveling crane was issued. This invention was followed by the first powered overhead conveyors in 1919 and then by the introduction of the first small electric hoist in 1940. These innovations were underpinned by basic mechanical concepts: to lift and move loads overhead, simply apply the rules of physics to overcome gravity to lift and friction to travel. All that was required to lift, lower and transport loads was ample horsepower and torque combined with sufficient gearing and reeving to provide the needed mechanical advantage.
The Benefits of Overhead Lifting
Just like the mathematical formulas for overhead lifting, its benefits are also readily apparent and well-documented. Overhead lifting utilizes unused overhead space to move and lift loads. The loads do not have to move within a predefined path, and large loads that do not fit down an aisle can be lifted and transported. Additionally, overhead lifting enables workers to move the loads at a safe distance.
With these benefits, overhead lifting has increased productivity and safety within a broad range of operations. Even applying overhead lifting to lighter loads improves the overall operational ergonomics and safety by eliminating strain on employees.
Overhead Lifting Components Get Smarter
Overhead lifting employs such well-known components as motors, gears, drums, sprockets, wire rope, and chain. Now, with the advent of digital intelligence, and the Internet of Things, the digital revolution has ushered in a cast of smarter components. Sensors, software and digital controls all create better efficiency with speed controls; improved safety due to motion controls; and enhanced performance through predictive analytics and energy conservation.
Examples of such emerging technologies and their benefits include:
- Smart controls, which control speed and acceleration for high-speed movement with precise positioning.
- Radio controls for operation at a safe distance from the load.
- Automation, which can be semi- or fully automated, for automatically picking and placing loads.
- Zone control to keep cranes outside of a predefined designated area.
- Analytics, diagnostics, and predictive maintenance that provide preventative service information before there is a breakdown.
- Controls that improve the overall lifting and traveling safety. These include anti-sway control, off-center hook detection, anti-collision, and overload detection systems.
- Regenerative braking that adds electric power back into the line and conserves energy.
Digital Overhead Technology Increasingly Affordable
Recent trends and developments in digital controls have made these new systems affordable, and, in many cases, standard on today’s advanced crane, hoist and monorail systems. Although investing in new technology can be intimidating, early adopters often reap the reward of competitive advantage. As an article written by Forbes Technology Council stated: “Investing in digitization may seem costly, but the financial losses that may incur by not transforming can cost even more… digital transformation is no longer an option but rather a necessity.”
Steel, aluminum, and metal processing companies are among the first to adopt hoist and crane innovations, according to an article on overheadlifting.org written by the Electrification and Controls Manufacturers Association (ECMA). The article notes an increasing interest to capitalise upon these digital technologies in smaller, lighter use manufacturing, production, and warehousing applications. “In addition to safeguarding personnel and facility structures from accidents, these safety enhancements add an extra layer of protection when an overhead handling system is being controlled by newer or less experienced operators,” the article states.