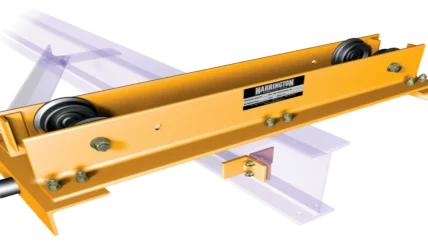
Harrington Hoists, a provider of lifting solutions for industrial applications, has supplied overhead cranes for underground maintenance bays designed to improve servicing efficiency in mining operations.
The maintenance bays allow heavy equipment and haul trucks to be repaired on-site, eliminating the need to transport machinery to surface workshops and reducing operational delays.
In a LinkedIn post, Harrington stated: “These bays allow mine equipment and haul trucks to be fully serviced or repaired without the hassle of hauling them back to surface shops. By constructing these bays with Harrington cranes at strategic points throughout the mine tunnel footprint, operations stay efficient and downtime is minimised.”
The maintenance bays are equipped with Harrington overhead cranes, which facilitate the lifting and manoeuvring of mining equipment within underground spaces. By integrating lifting systems at strategic points within tunnel networks, mining companies can conduct repairs without disrupting production schedules.
Harrington operates as part of Kito Crosby, a supplier of hoists and cranes used across multiple industries. The company provides a range of material handling equipment, including electric and air-powered chain hoists, wire rope hoists, manual hand chain hoists, and below-the-hook lifting devices.
In November 2023, Kito Crosby expanded its product line with the launch of hazardous location three-phase electric chain hoists for environments with flammable gases or combustible dust.
According to Harrington, the new models include the RNER2, RNER2B, and RNER2D.
The RNER2 model complies with Class II Division 2 standards, providing dust group protection for coal and grain dust. The RNER2B model is designed for Class I, II Division 1 environments, offering protection against ethylene, propane, coal, and grain dust. The RNER2D model meets Class I Division 2 standards, making it suitable for hazardous gas environments containing hydrogen, ethylene, and propane.