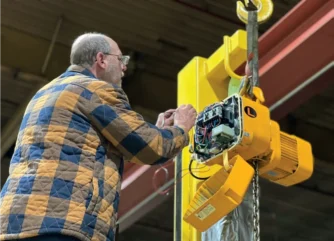
OCH: Will Dunn, LES, USA, what changes in US standards and regulations have you seen recently and how does this differ from other regulations outside the US?
WD: The landscape of manufacturing standards in the US versus Europe has clearly defined differences, but with a similar core goal; safety above all. The differences are typically shaped by cultural and data-driven conclusions with some conflicting opinions on both sides of the pond In the United States, manufacturing— particularly in the field of lifting and rigging equipment—holds a unique position. It’s characterized by stringent standards, a deeprooted culture of innovation, and a focus on safety that distinguishes it from practices in other regions.
Historically, the US has been at the forefront of technological advancements, and this is reflected in the manufacturing standards and procedures carried out today. With an ‘America First’ mentality it is widely regarded that anything made in America is of significantly higher quality than those imported from foreign countries, and I have to agree- with litigation being second nature and ever-rising liability insurance costs, it pays to over-engineer products to ensure they can take a beating in the toughest of applications, and in this country strength and reliability is everything.
Having operated in both the US and Europe a clear difference is the amount of proof testing that is second nature and demanded by some of the regulations as a minimum requirement for that piece of equipment to undergo its initial use. In Europe it is standard practice for equipment such as Web Slings, Round Slings and Chain Slings to be picked and shipped with a Declaration of Conformity (or Report of Through Examination depending on timings) stating the EN standard, it’s working load limits, minimum break strength, safety factor etc. But with no load test. In America those items are typically subject to a load test that exceeds the working load limit and then fully certified in order to provide proof that the equipment is fit for purpose, hence the name “Proof Load Test”.
OCH: How do these differences effect your business?
WD: Something I have noticed in the US that I have never seen in Europe is one of our manufacturers going the extra mile and actually filming the test on camera for the ultimate peace-of-mind and solid record of proof, making that footage available to the purchaser as well as holding a copy on file, and to me it makes complete sense because quite simply anyone can produce a fake test certificate or attest that it was subjected to the correct procedures, but “seeing is believing” as one wise customer once told me. I am a huge advocate for this procedure and think it’s time more manufacturers integrate this type of absolute proof into their testing regime, not only does it protect the manufacturers from falsely being held responsible for an equipment failure, it also holds to account those members of the team who are responsible for carrying out the test to the appropriate standard.
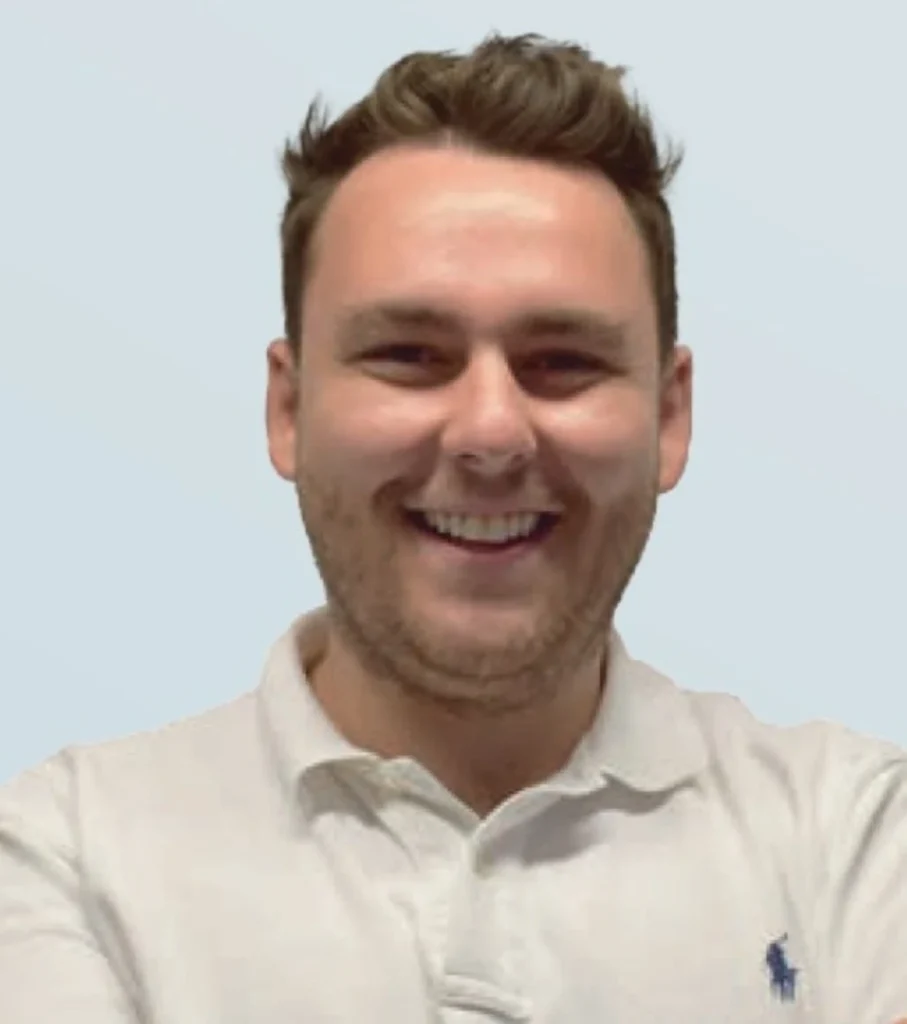
One thing that does surprise many though, is the differences in design factors (safety factors to the Europeans reading) in the US Vs. Europe, for example; a Web Sling is in Europe is required by BS EN 1492-1 standard to have a 7:1 design factor, yet in the US under ASME B30.9 this is lowered to 5:1. Leaning in on culture differences and data-driven decisions might be where we uncover the answer to what on the surface appears as a ‘lesser’ requirement- ASME B30.9 requires that all slings are proof load tested prior to their initial use whereas in Europe the BS EN 1492-1 standard does not require that each and every sling is proof load tested, simply being manufactured to the standard is deemed sufficient, and since operating stateside I am not sure I agree wholeheartedly with that process, I feel it could benefit from a little stateside inspiration. However, with that said, having played the role on both sides of the pond, I do recognize the complexities this poses on distributors that stock this type of product in Europe including extended lead times and investment in to testing equipment, but we do have a responsibility to uphold in this industry, and going above and beyond should be the norm. Having held this discussion with fellow Europeans in my network, the debate often holds strength on both sides with those who oppose the B30.9 guidance pushing back and voicing that proof load tests often exceed the working load limits and by doing so could be thought to impact the strength of the sling, but I politely rebuttal the suggestion and show them the OSHA website: “Proof testing at 200% SWL repeated every 90 days will have no detrimental effect on the strength of the sling. Tests conducted by Boeing have shown that nylon web slings can withstand severe and frequent repeated tests at loads of over 550% SWL with a strength loss of less than 2%” (OSHA standard interpretations 1988-07-19). The debate tends to come to a grinding holt at this point either in acceptance or disbelief of the facts.
The bottom line is that regulation and standards in manufacturing in the US Vs. Europe are very similar in my opinion, they take different approaches with common goals revolving around safety and protection, with the US leaning towards an area of absolute proof and Europe leaning towards a more initially costeffective trust and honesty-based system with additional ‘padding’ to protect against breaches. I think it’s obvious, but personally I am in favor of the US-system.
OCH: Mark Yerse, CMCO, what changes in US standards and regulations have you seen recently?
MY: We’ve been actively involved in updating ASME and ISO standards, which enhance the safety and competitiveness of lifting, chain, and rigging products. We’ve also been adapting to the Department of Energy’s revisions to motor efficiency standards. Additionally, there have been significant updates to environmental regulations, including the Toxic Substances Control Act and the European REACH regulations, along with global efforts to eliminate Persistent Organic Pollutants. Cybersecurity standards are also rapidly evolving, presenting both challenges and opportunities for us to deliver a premium customer experience by leveraging Industry 4.0 technologies
These changes align closely with our commitment to creating safer, more productive, and sustainable products and solutions. They also support our mission to develop intelligent motion solutions that move the world forward and improve lives. Adapting our products to meet these new regulations requires investment, but it also drives meaningful progress in environmental stewardship, workplace safety, and community engagement.
OCH: How does this differ from other regulations outside the US?
MY: While other countries and regions have standards and regulations similar to those in the US, they do differ in some respects. Columbus McKinnon is actively involved in developing these standards worldwide and ensures that our products meet the requirements in every market. In the US, the American Society of Mechanical Engineers (ASME) publishes the B30 standards titled “Safety Standard for Cableways, Cranes, Derricks, Hoists, Jacks, and Slings,” which set safety requirements for hoists, cranes, and related equipment. These standards are widely accepted across all states.
In addition to complying with mandatory standards and regulations in each country— which include essential design rules and required verification tests—Columbus McKinnon has developed robust internal design practices. Over the years, we’ve refined our analytical and experimental modeling techniques and established evidence-based processes to ensure our products perform at a superior level. We’ve also embraced best-in-class continuous improvement methods to regularly evolve our products and processes.
OCH: When launching new products, what processes do you have to go through to ensure your equipment is safe and ready to be installed?
MY: At Columbus McKinnon, product safety is our top priority. During the new product development process, each part and assembly undergoes rigorous testing to ensure it will perform safely under conditions that exceed those it will encounter in the field. We also subject final assembly prototypes to similar testing, ensuring they meet both our internal standards and all applicable codes and regulations. A new product doesn’t go to market until all safety and testing requirements are fully satisfied.
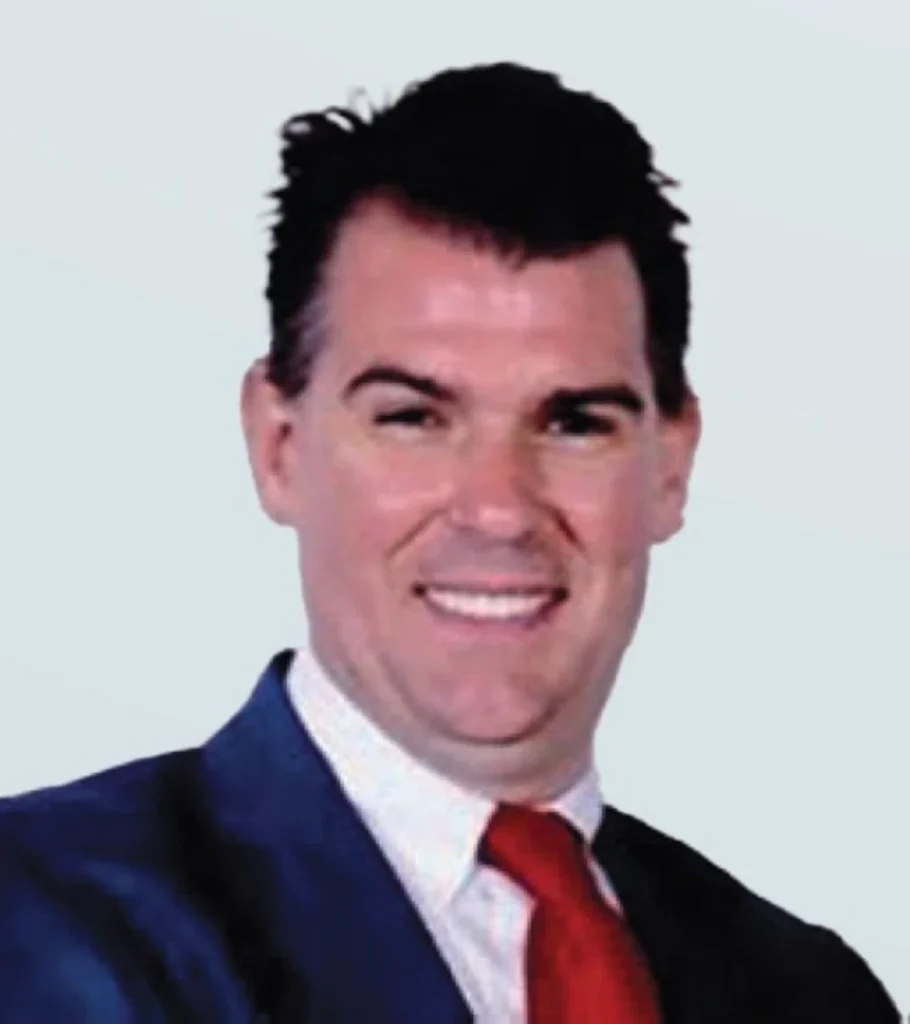
OCH: Arnie Galpin, Spanco, what changes in US standards and regulations have you seen recently?
AG: Key players within our company joined a task group to help author the new Jib Crane design standard, CMAA 76, soon to be released by the Crane Manufacturers Association of America part of MHI the largest material handling, logistics and supply chain association in the US. (Galpin has been involved with CMAA and ANSI for over 20 years).
The new Jib Crane standard defines all the stress and deflection limits that the engineers need to follow to keep the workers safe when using the crane.
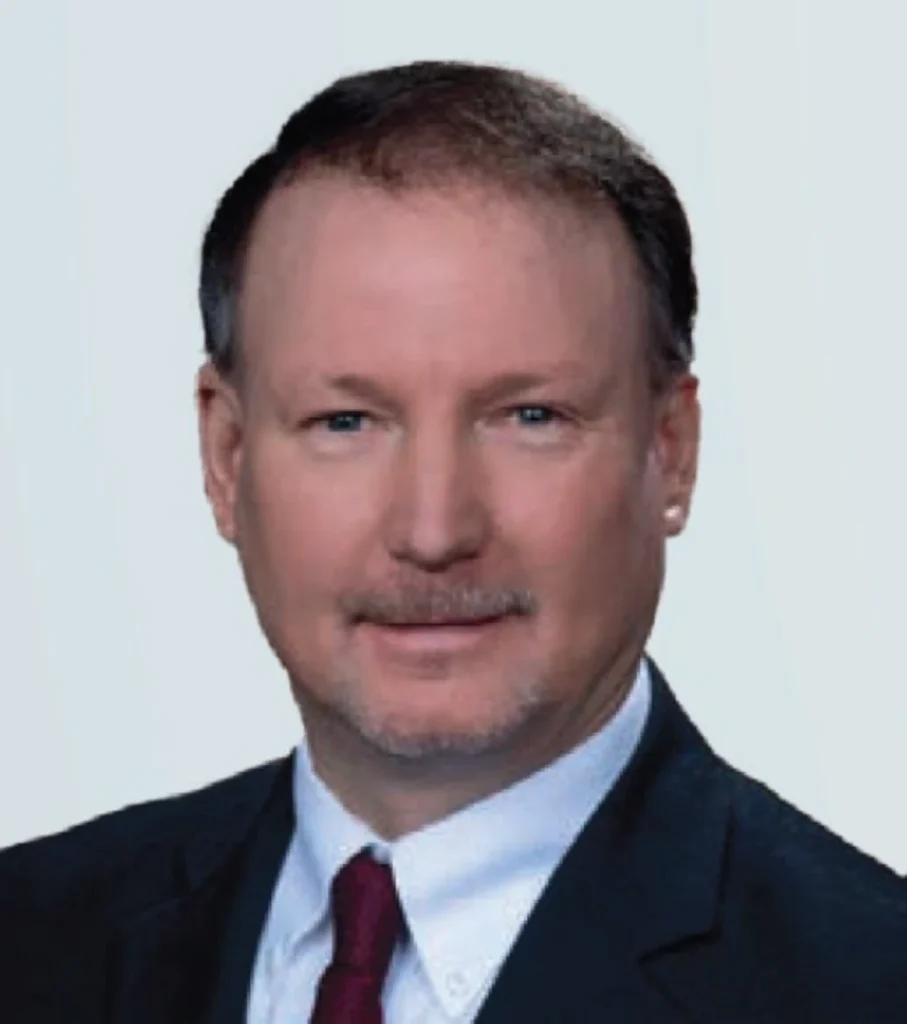
A jib crane designed to this new standard will provide years of trouble-free performance and be ergonomically safe for optimum operator use and performance.
OCH: When launching new products, what processes do you have to go through to ensure your equipment is safe and ready to be installed?
AG: We review all the critical-use parts with FEA, Finite Element Analysis, leveraging computer analysis to evaluate stresses and stress concentration points during our products’ concept and design phase. During product validation, we conduct rigorous cyclical testing on high-use components to prove their durability and fatigue stress resistance.
OCH: Ashley Larochelle, CraneWerks, what changes in US standards and regulations have you seen recently?
AL: Safety in the overhead crane and hoist industry is a topic that continues to evolve, driven not only by regulatory standards but also by a growing awareness among consumers about the importance of workplace safety.
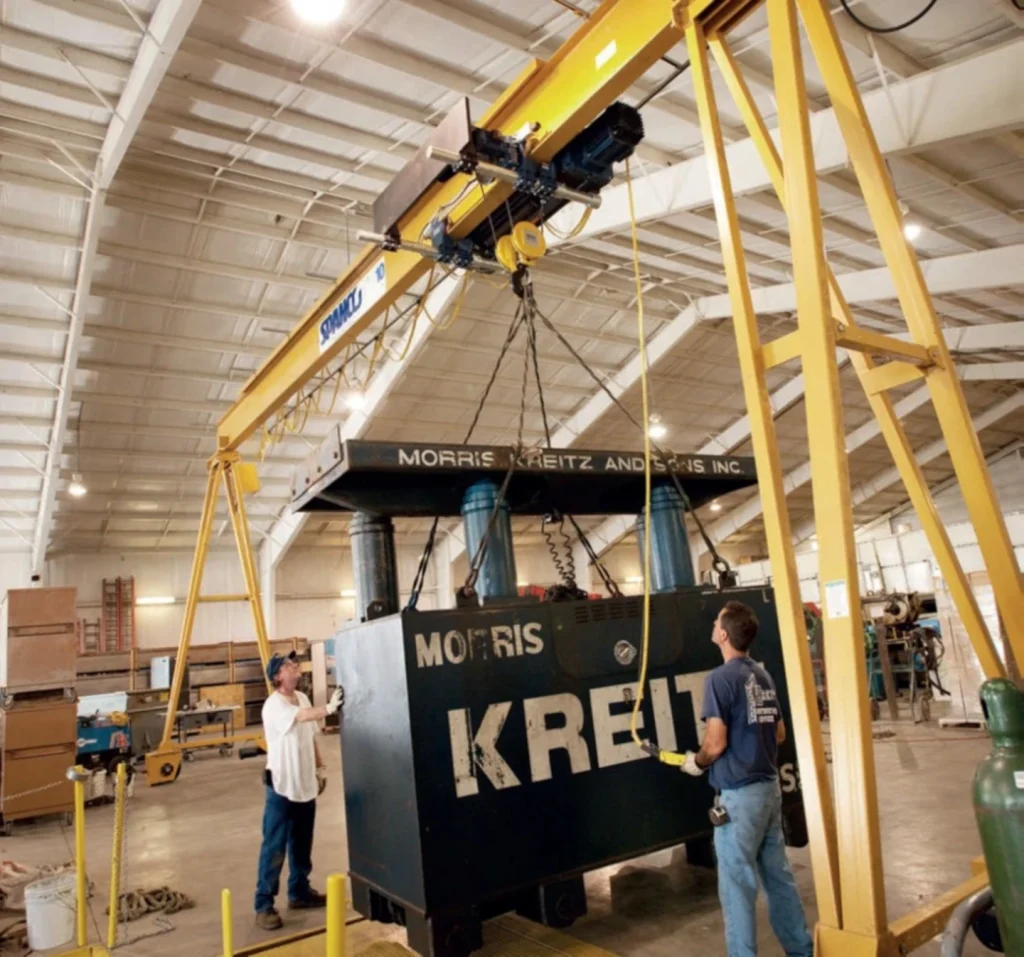
While U.S. standards and regulations, such as those established by OSHA, ASME, and CMAA, have remained relatively stable over the past decade, we’ve observed a significant shift in how businesses approach safety—particularly in response to the challenges posed by increasing technology dependence and automation in other industries.
However, the real transformation we’ve witnessed isn’t in the regulations themselves but in the heightened safety consciousness among our customers.
OCH: How does this effect your business?
AL: As a leader in the overhead crane and hoist industry, CraneWerks is aware that manual labor remains a critical component of daily operations. Unlike industries rapidly moving toward full automation, our customers still rely heavily on human interaction with machinery. This reliance on manual labor brings unique safety challenges, especially as technology becomes more integrated into the workplace. The rise of digital tools and automation in adjacent industries has led to a paradoxical increase in risks within our field. Workers are more prone to distractions, which can increase the potential for accidents.
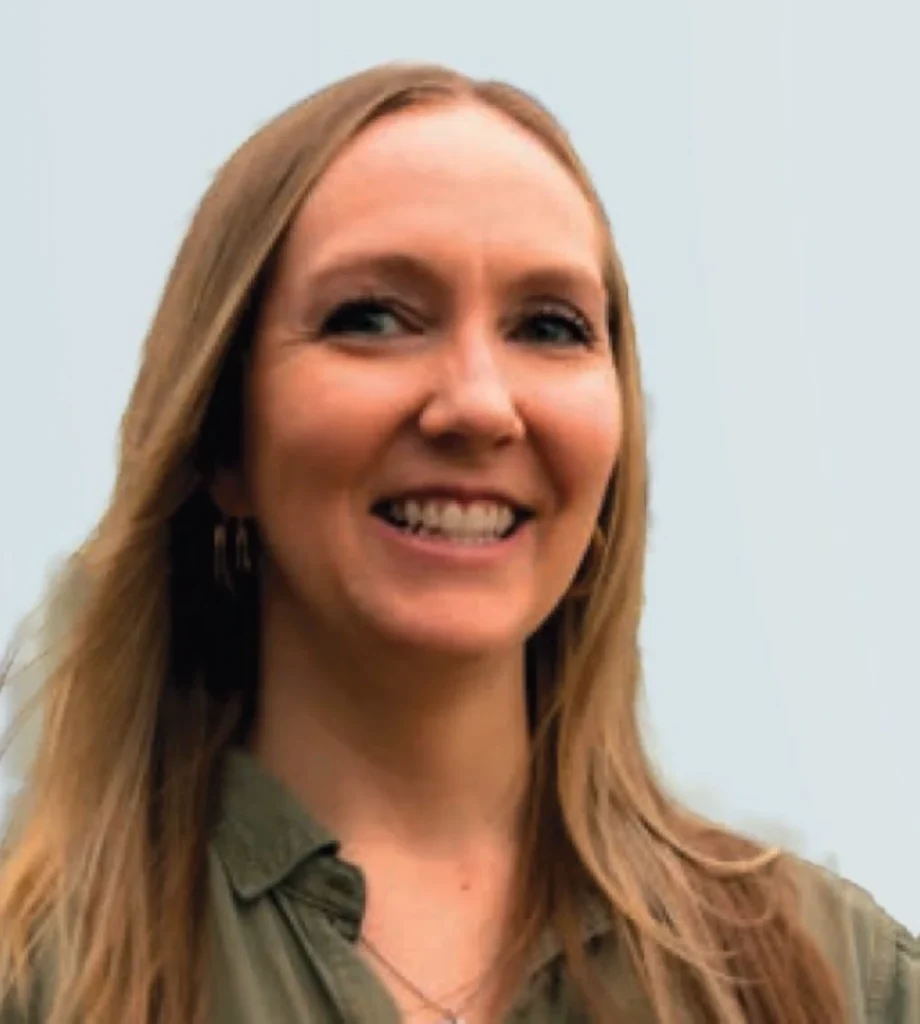
As a result, we’ve seen an uptick in requests for safety features designed to mitigate these risks. Customers are increasingly asking for lights around hoist hooks to improve awareness, similar to those installed on Powered Industrial Vehicles (PIVs). Overload protection systems are being requested more frequently, with the desire for settings below the rated capacity—moving away from the standard limits that would engage between 100-125% of the equipment’s rating. In addition, requests for collision avoidance technology, side-loading prevention, antisnagging, and anti-sway mechanisms have been incorporated into plant safety standards.
CraneWerks has partnered with companies like Magnetek to install and test some of this equipment in our own facility. These features, once considered optional, are now becoming standard as businesses strive to protect their workforce and minimize downtime caused by equipment damage.
Moreover, the trend toward reducing physical exertion in the workplace continues to drive safety considerations. As the recognition grows that repetitive lifting can lead to fatigue and injury, corporate policies are shifting to limit the loads employees are expected to lift manually. This change presents a significant opportunity for CraneWerks, as we offer solutions such as lifting devices and custom manipulators that reduce the physical burden on workers while maintaining productivity.
OCH: How does this differ to other regulations outside the US?
AL: While CraneWerks focuses exclusively on the U.S. market, we are aware that international regulations may differ significantly. However, the underlying principle remains the same: safety is paramount, and businesses must adapt to ensure their workers are protected in an increasingly complex and technology-driven environment.
In summary, although U.S. safety standards in the overhead crane and hoist industry may not have changed drastically, the approach to safety has evolved significantly. CraneWerks is more aware than ever of the need to integrate advanced safety features and reduce the risks associated with manual labor, creating new opportunities for us to provide innovative solutions that meet these demands.
What changes in U.S. standards and regulations have you seen recently – if none, when were these last established? If so, what impact and benefits have these made in the market?
KP: Standards are constantly updated to reflect the needs of industry and regulators. It is up to each industry or regulatory agency to determine the standards that best fit their needs. The American Society of Mechanical Engineers (ASME) is an independent, not-for-profit organization. ASME is one of the oldest and most respected standards developing organizations (SDOs) in the world. It produces and maintains approximately 550 codes and standards, covering a multitude of technical areas including boiler components, cranes, elevators, hand tools, fasteners, and pipelines to name just a few.
ASME has over 30 safety consensus standards that are related to the crane industry, including the B30 Safety Standards Committee for Cableways, Cranes, Derricks, Hoists, Hooks, Jacks, and Slings and P30 Planning for the use Of Cranes, Derricks, Hoists, Cableways, Aerial Devices and Lifting Accessories volumes, as well as the BTH-1 Design of Below-the-Hook Lifting Devices. These standards are developed by a consensus committee made up of industry experts and are continuously maintained. Some have been recognized, either in whole or in part, by governmental or regulatory agencies around the world.
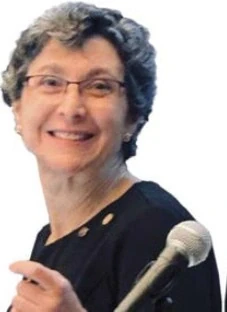
Standards offer substantial value to organizations and end users: Standardization can help maximize compatibility, interoperability, safety, repeatability, and/or quality in product development and processes, while increasing efficiencies (e.g., training) and minimizing waste.
How does this differ to other regulations outside the U.S., and do they change from state to state?
KP: ASME standards are considered voluntary because they serve as guidelines, but do not of themselves have the force of law. Their use is voluntary. Standards become mandatory when they have been incorporated into a business contract or into regulations. Each jurisdiction decides independently which of the regulations or codes are required within their jurisdiction. ASME does not keep track of regulations in place for the jurisdictions in the U.S.
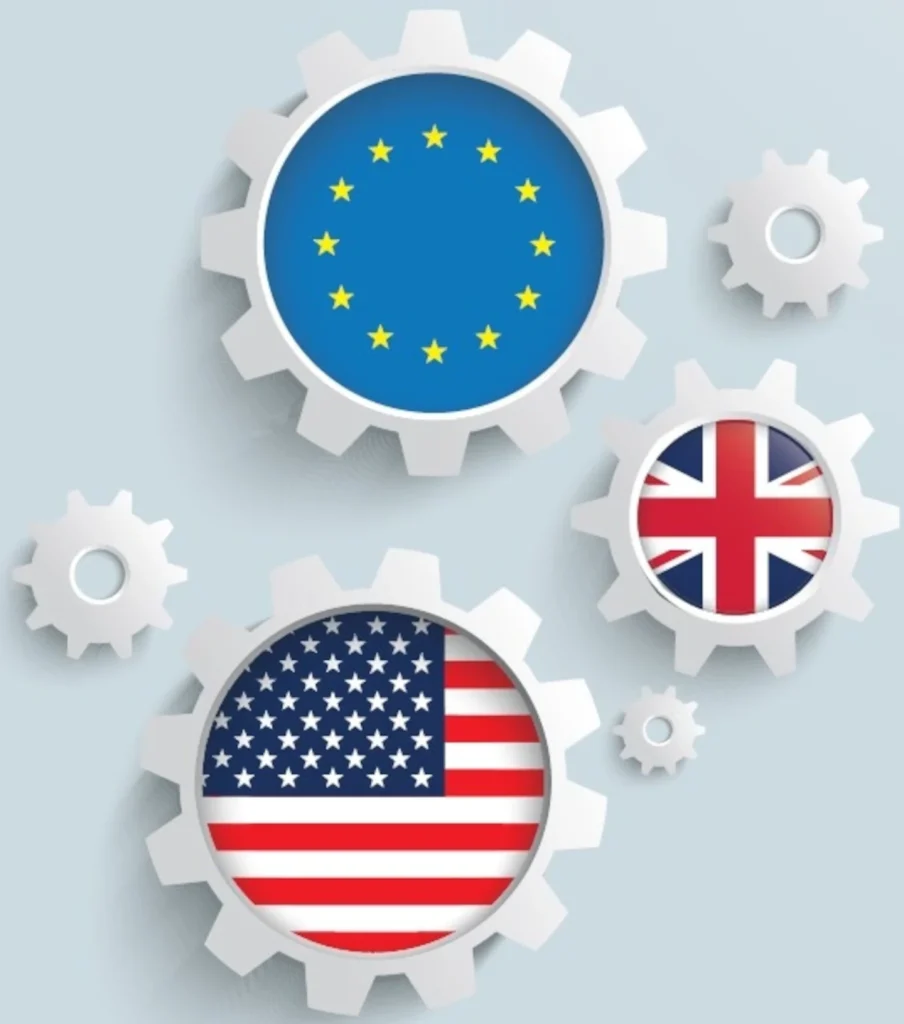
When companies launch new products, what processes do they or should have to go through to ensure their equipment is safe and ready to be installed on site? Also, is ASME involved in this process?
KP: ASME standards staff does not ‘approve’, ‘rate’, or ‘endorse’ any item, construction, proprietary device, or activity; Therefore, we are unable to answer any questions that might be interpreted as doing so. In addition, ASME does not offer certification programs associated with B30, P30 or BTH; however, if there is a need for product certifications related to cranes and hoists, ASME Conformity Assessment staff can be contacted to find out about creating a path to certification for these standards and the important industry they relate to. In the lifting handling industry, individuals also may consider consulting third body certification bodies and/ or qualified experts to ensure compliance with appropriate standards. For other products, such as boiler and pressure vessels, ASME’s Conformity Assessment (CA) Certification and Accreditation programs have helped leverage the playing field for many businesses, enabling them to enter new markets, compete, and win. Certification helps companies comply with regulations, achieve process efficiencies, reduce costs, and increase their product’s quality, safety, and reliability.
Are there standards or regulations you would like to see introduced in the near future?
KP: ASME is open to developing new standards and certifications based upon the needs of the industry and government. A request for a new standard or certification may come from individuals, committees, professional organizations, government agencies, industry groups, public interest groups, or from an ASME division or section and is evaluated by the appropriate area within ASME.