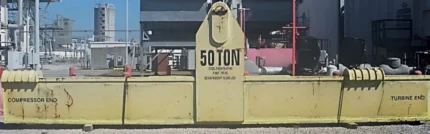
When your below the hook equipment fails an inspection or shows significant wear, deciding whether to modernize or replace it can be challenging. Making this decision is not a frequent occurrence in your workday. This decision often hinges on several factors, including budget constraints, usage patterns, equipment age and the value of the items being lifted.
To further complicate the decision, below the hook devices are unique because their wear and tear are not always visible, making professional inspection crucial which is going to be done offsite usually. To make an informed decision, you need a comprehensive evaluation that includes disassembly, thorough cleaning, detailed mechanical, structural and electrical analyses complete with comprehensive photographic documentation of the findings.
Ideally, the evaluation team you choose should also be able to address deficiencies or recommend new equipment to minimize downtime. Choosing a company that can offer both options will help you make the best decision for your company to modernize or replace the equipment.
Understand the Evaluation Process
Before diving into a decision, ensure you understand the inspection and evaluation process. Seek out a service that provides traceability and transparency, including detailed reports and photographs. The evaluation should involve no load operational testing of functions and safety features, a complete teardown and rigorous cleaning to assess the equipment’s condition accurately. Make sure the evaluation team communicates regularly, provides insights into their findings, and offers reliable recommendations.
Review your findings to make an informed decision you can stand behind
Now that you have the evaluation report, review it carefully.
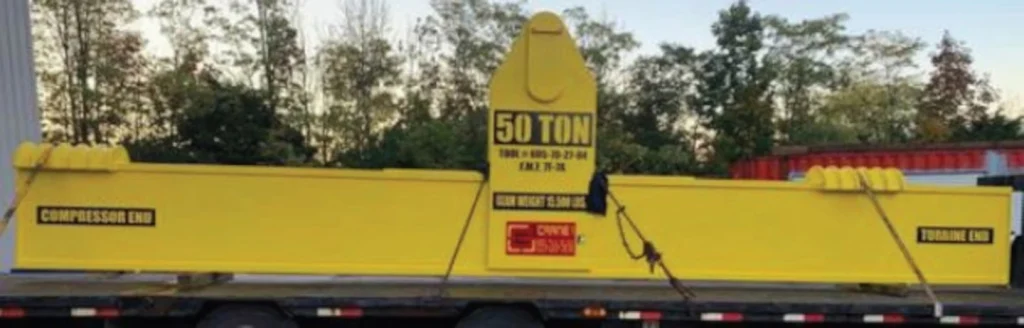
This document should detail the equipment’s current state, including:
- Repair History: Examine past repairs and maintenance records. Frequent repairs or significant wear might indicate that replacement is more cost-effective overall.
- Component Analysis: Look at the condition of key components such as shafts, brakes, gears, couplings, bearings, and clutches noting any signs of wear, alignment issues, or damage.
- Electrical Systems: Inspect wiring, cables, and electrical connections for signs of wear or deterioration.
Understanding these aspects will provide insight into whether the equipment can be effectively modernized or if a replacement is warranted.
Consult with the company who executed your inspection team to understand their recommendations and the reasons behind them. Compare the costs and benefits of modernization versus replacement. Additionally, consider the time each option will take.
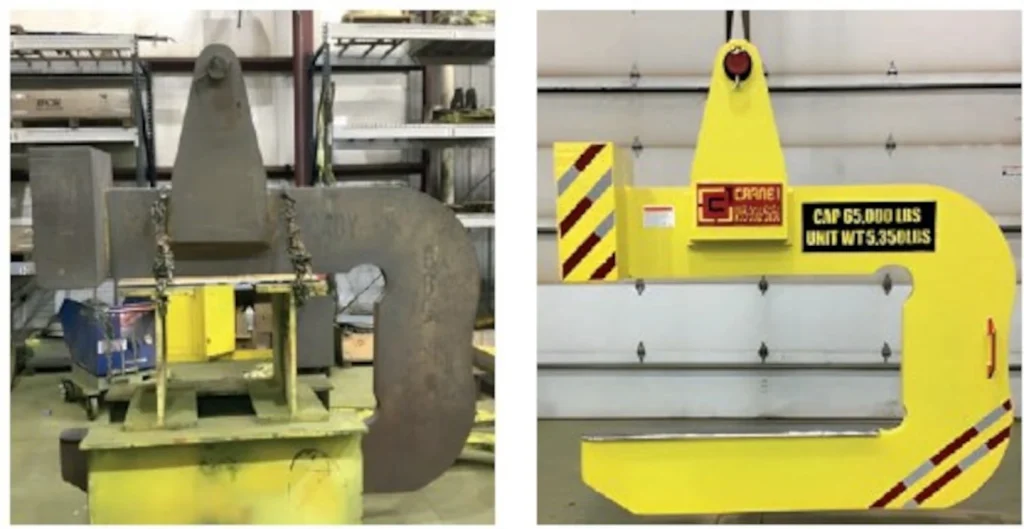
Meet with your Team
Getting your team’s insight is crucial. Engage with them to discuss these factors:
- Budget and Budget Allocation Limits: An itemized breakdown of the lifting device’s condition should be part of the evaluation. Capital expenditure budgets often have strict limits and the decision on whether to repair or replace should align with these constraints. Sometimes, decisions are driven by budget limits than by what is most cost-effective. Ensure you have a clear understanding of the capital expenditure budget and how it may impact your choice.
- Usage and Application: Assess how your company’s below the hook equipment is being used. Consider the intended use, frequency of use and whether there are any changes in the utilization of the equipment compared to what it was originally purchased to do. Evaluate what types of loads the equipment handles, ranging from as little as 50 pounds to over 350 tons. Analyze the lifting points and ensure the equipment’s design is suitable for your specific needs. Also, consider the training level of your staff and whether they are using the equipment within its standard limitations. The environment in which the equipment operates is also crucial—examine factors like space constraints, flooring material, and temperature ranges.
- Repair History and Maintenance: Review the equipment’s age and its repair history. Check for any previous repairs, discrepancies and stress fractures that were corrected. Assess how regularly the equipment has been maintained and inspected. Look into the condition of critical components like shafts, brakes, gearing, couplings, bearings, and clutches. Identify any signs of wear, alignment issues or damage. Inspect electrical components for issues such as cracked wires, poor insulation, and faulty cord grips. Understanding the repair history will help gauge whether continued maintenance is viable or if replacement is more cost-effective.
Compare Modernization and Replacement
Weigh the time required for modernization against the lead time for ordering and installing new equipment. For example, if modernization takes four months and replacement takes 18 months, consider which option better fits your operational needs. Creating a pros and cons list with your team can be a helpful exercise to visualize the trade-offs. Factor in not only the cost but also the impact on operations, potential downtime, and long-term benefits.
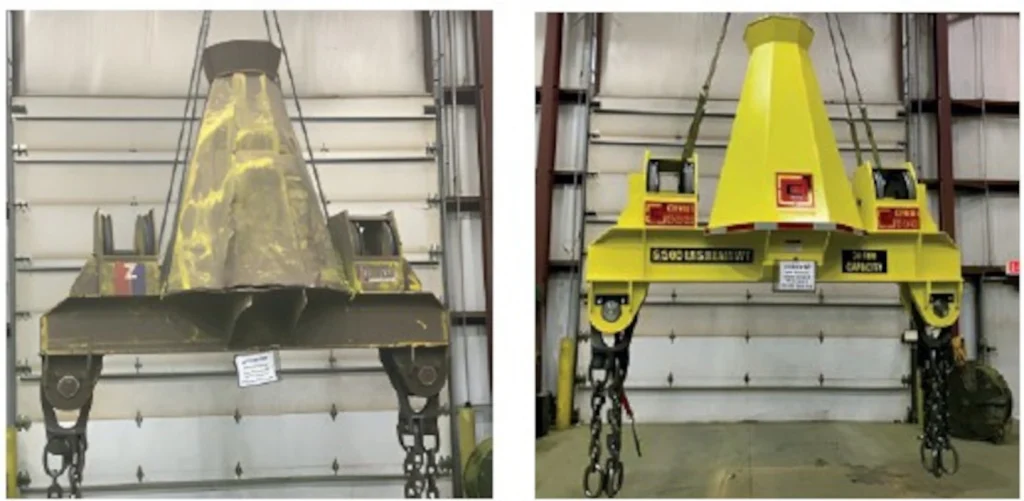
Modernization Timeline: Assess how long it will take to modernize the existing equipment. This includes time for disassembly, repairs, recertification, and reinstallation.
Replacement Timeline: Determine the lead time for ordering, manufacturing, and installing new equipment. Consider any potential delays in delivery or installation.
If you decide to modernize your equipment, ensure you will receive a Re-certification Report. This report should confirm that the updated equipment meets current standards and is safe for continued use. It should include detailed documentation of any modifications, improvements, and testing results. This certification is essential for ensuring that the modernized equipment is dependable and compliant with industry regulations.
Making the Final Decision
After evaluating all factors—condition of the equipment, usage, budget constraints and time considerations—make your decision based on a balanced view of immediate needs and longterm goals. If you choose to repair or modernize, ensure you obtain a re-certification report confirming the equipment meets current safety and performance standards. If replacement is the chosen path, collaborate closely with suppliers to ensure you get equipment that meets your current and future operational needs.’