
Hoosier Crane was tasked with finding a material handling solution that would maximize floor space and improve ergonomics for operators while handling and storing bundles of material. Through several phases of design and collaboration, the Hoosier Crane team engineered, fabricated, and installed a telescoping stacker crane to meet the client’s needs.
The stacker crane features a three-stage telescoping mast that collapses overhead to transport materials above the storage area and eliminates the need for dedicated transportation aisleways. The mast extends to the floor and can rotate 360 degrees continuously to load and unload materials from any direction and at any height above the ground. The mast is rigid to allow the operator to reach into multiple levels of shelving while maintaining the stability of cantilevered loads.
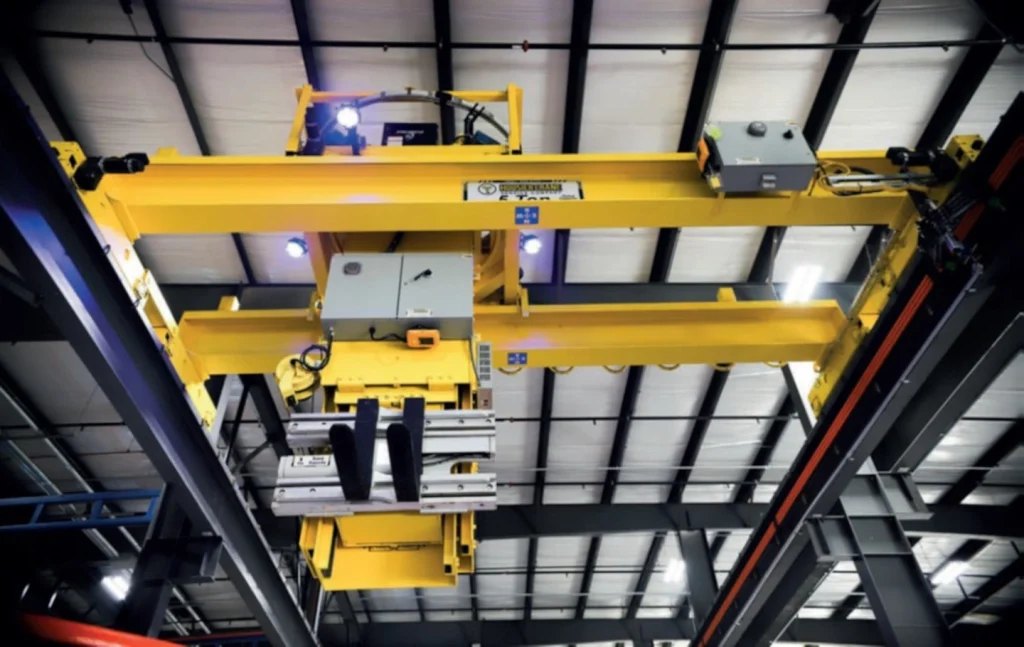
“I was tasked on creating a very special material handling solution for a local customer. Working with our engineering team and the customer we came up with a concept. Our engineering team was able to hammer out all the specific details and design requirements so that our fabrication shop and engineers made the concept a reality,” explained Jon Harkrider, VP, sales, Hoosier Crane.
“We now have a happy customer and another quality product out in the field.”
One of the challenges with this project was minimizing the footprint of the mast and forks to maximize the floor space for storage.
Hoosier Crane was able to provide this solution with a footprint that is 77% smaller than a traditional forklift of the same capacity, allowing the client to minimize aisle widths and increase the amount of material stored per square foot.
To accomplish this, many of the mechanical components for this system are located within the mast itself. This includes an R&M wire rope hoist, a hydraulic power unit that powers the fork positioner, and precision machined rails and bearings that guide the mast up and down.
There are many access holes and modular parts that can be reached while the crane is in service, allowing for preventative maintenance and inspection without major teardown operations.
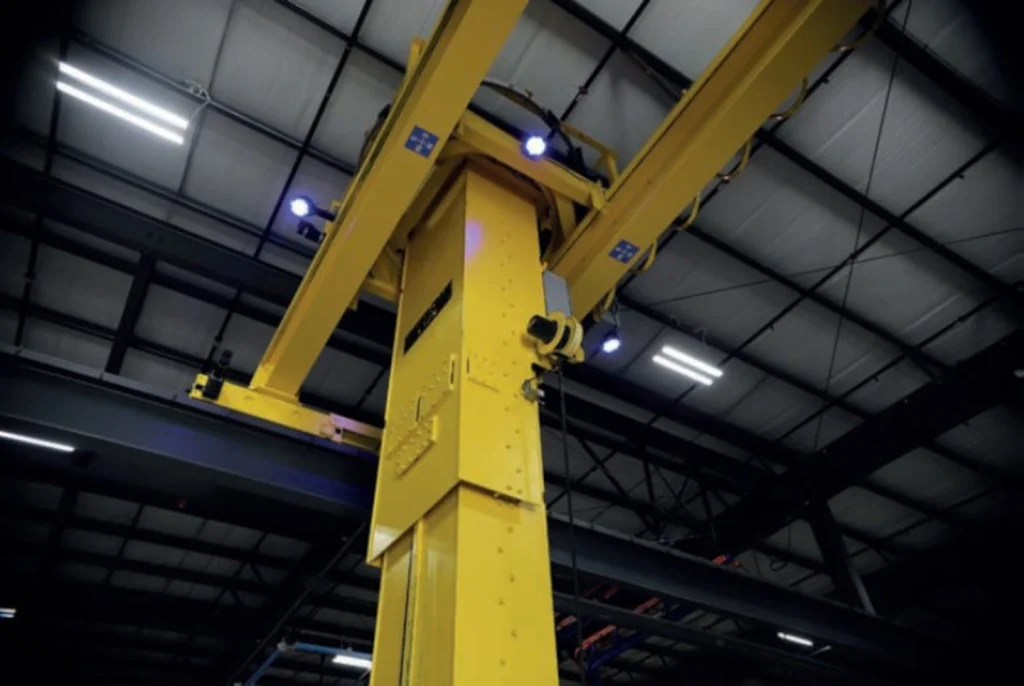
“This stacker crane was a highly technical project that our team made happen and was a very challenging job because our engineers had a very tight timeline from concept to a fully functional product. They wanted many features built into a small footprint,” added Harkrider.
“It’s always great to meet our customers’ expectations. We have many challenging projects coming up and are always looking to solve other material handling issues.”
When handling overhead loads, safety is always of great concern. The stacker crane is engineered with minimum 3:1 safety factors throughout and is designed to limit fork deflections to 1/8” under full load.
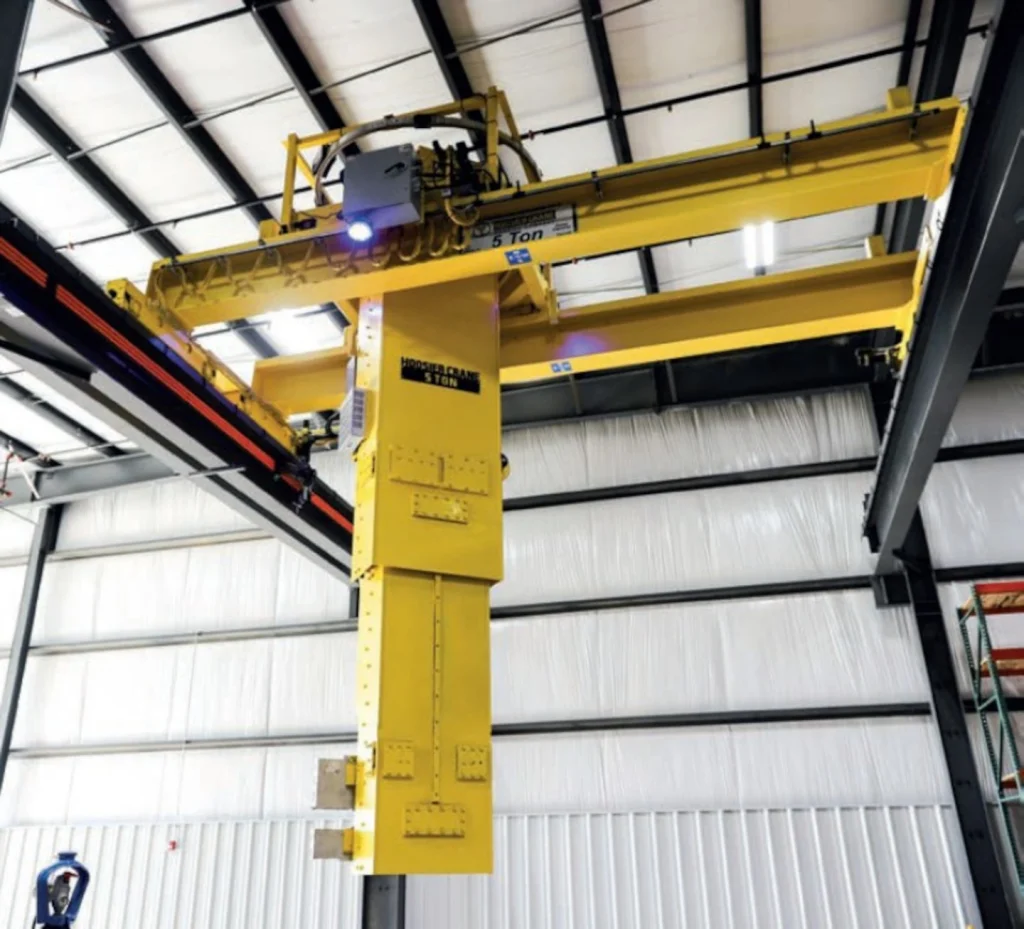
One of the key components in limiting deflection is the high-capacity rail and bearing system which is also critical to the smooth operation of the mast. In addition, the crane was equipped with safety lights and warning horns to warn workers of crane travel overhead. The safety lights display a blue box on the floor that provides a visual boundary for safe work and operation. All functions are controlled by a radio remote control, allowing the operator to operate the crane from a safe position.