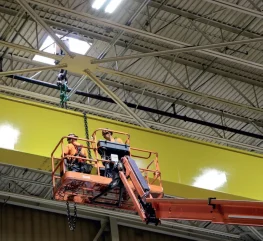
Hoosier Crane recently partnered with BuhlerPrince to increase the capacity of its runway and column structure, removing and installing a new power bar system, removing two 50 ton top-running double girder bridge cranes, and installing two 67.5 ton top-running double girder bridge cranes with Magnetek Tandem Radio Control System.
The reason behind the upgrade was that BuhlerPrince needed to increase the capacity in one of its manufacturing areas to handle a new line of products. To accommodate this, Hoosier Crane removed two existing 50-ton top-running double girder bridge cranes.
The company, based in Holland, Michigan, USA is part of Buhler Die Casting, in Uzwil, Switzerland and is North America’s leading die casting machine manufacturer. Their products cover machines from 300 ton to 10,000 tons of clamping force, services for retrofit and remanufacturing, spare parts and service and support to the die casting industry.
“It was the first time we worked with this client and Hoosier Crane's biggest order to date. They contacted us and after discussing their needs we drove to the site in Michigan taking pictures and measurements, capturing all the fine details of the upcoming project. Then we came back to the office where we worked on the proposal and were granted the project. Having the opportunity to be onsite and visit them in person was invaluable,” said Brian Koziatek, inside sales manager, Hoosier Crane Service Company.
“There was a lot going on with this project in particular, but it was a soft landing as far as finalizing it, performing the work and completing the installation for them. It was a unique thing. But what's worked out even better is that thanks to the success of the project we are in consideration for a new plant at BuhlerPrince scheduled for 2025/2026, as they are expanding.”
As part of the installation, the Hoosier Crane team worked with a mobile crane and operator to access a roof hatch to lift and lower two 67.5 ton top-running double girder bridge cranes with Magnetek Tandem Radio Control System.
“We had four guys inside the facility, guiding the mobile crane and operator through the roof hatch, communicating with them to land the cranes and make everything happen. The initial start of the project was taking down two existing 50 ton cranes, so we had workers in there cutting the steel, dismounting the components, taking it apart piece by piece,” said Koziatek.
“Once the existing cranes were dismantled and taken away, that gave us more room to do the other work, so we upgraded the conductor power bar system and installed the structural runaway steel and column upgrade. Our team was there for approximately a month, welding steel plates and beams to the existing structure to increase capacity, because the 50 ton cranes were no longer suitable for the new dies they were building for a client.
“To increase the capacity of the runway structure, we installed two 67.5 ton top-running double girder bridge cranes, again with a mobile crane and operator outside that's going through the roof hatch, guided by our team. It was a big undertaking with only about four or five inches of clearance above the cranes, so it was very critical on the design of the crane.
“Everything had to be done precisely and accurately, for everything to fall into place so gracefully, you think about all this weight landing and getting picked up in the air, but everything just landing like a feather is really remarkable.
“Magnetek is one of the world leaders in wireless radio controls and other controls, and we're a major dealer for them and they supplied the wireless radio control systems that were used in this project.”
Koziatek who has worked for the company for seven years said the industry is changing every day and the focus is on safety more than ever before.
“There's this new breadth of automation in removing operator error. We’re seeing this increase of getting the operator out of the way, and having some of these crane systems fully automated where you're pressing a button in a location and the crane is programmed to make the pick and do everything it needs to do and stay out of different areas, protective zones,” he said.
“There's lasers and remote control radio systems like Magnetek. There’s all types of technology now available to automate the crane and make it as safe as possible. My job is to find out what requirements the end user needs, and then design and quote everything from the bridge crane to every piece of it, whether it's the runway steel, the columns, support structure, power bar, rail system, and the equipment for install, and the manpower.”
Hoosier Crane is a family-owned business headquartered in Elkhart, Indiana. Its services include parts and new equipment sales, in-house manufacturing, 24/7 crane service, and overhead crane training.