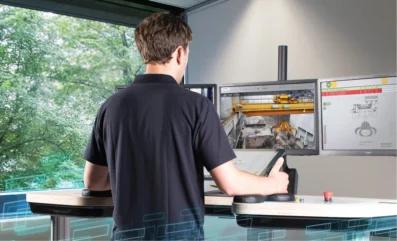
OCH: Can you give an overview of your product.
Roland Najbar, Business Development Cranes, Siemens Industry: The SIMOCRANE Crane Management System (CMS) by Siemens is a comprehensive solution designed to optimise crane operations in industrial and port environments. It provides real-time data visualisation and analytics, allowing operators, maintenance teams and managers to monitor crane performance effectively and make informed decisions. It offers flexibility because it’s available as both a centralised and de-centralised (local) solution, and can be integrated with other automation (even non-Siemens) systems. Typically, a SIMATIC PLC (crane operating PLC) integrates with Siemens robust SIMATIC industrial PCs, which run the SIMOCRANE CMS software. If a centralised solution is used, the data is communicated from the crane (can be via SCALANCE IWLAN or other methods) to a central server, where maintenance personnel and management has visibility over all of the distributed clients (cranes) simultaneously. The system is completely customisable to align with the work objectives on a day-to-day basis. CMS’s graphic interface is intuitive and transforms complex data into simple information, which enables the operator or maintenance personnel to take action quickly. In summary, CMS is a data-driven crane management system that aims to prevent time-consuming breakdowns, boosting operational efficiency and safety.
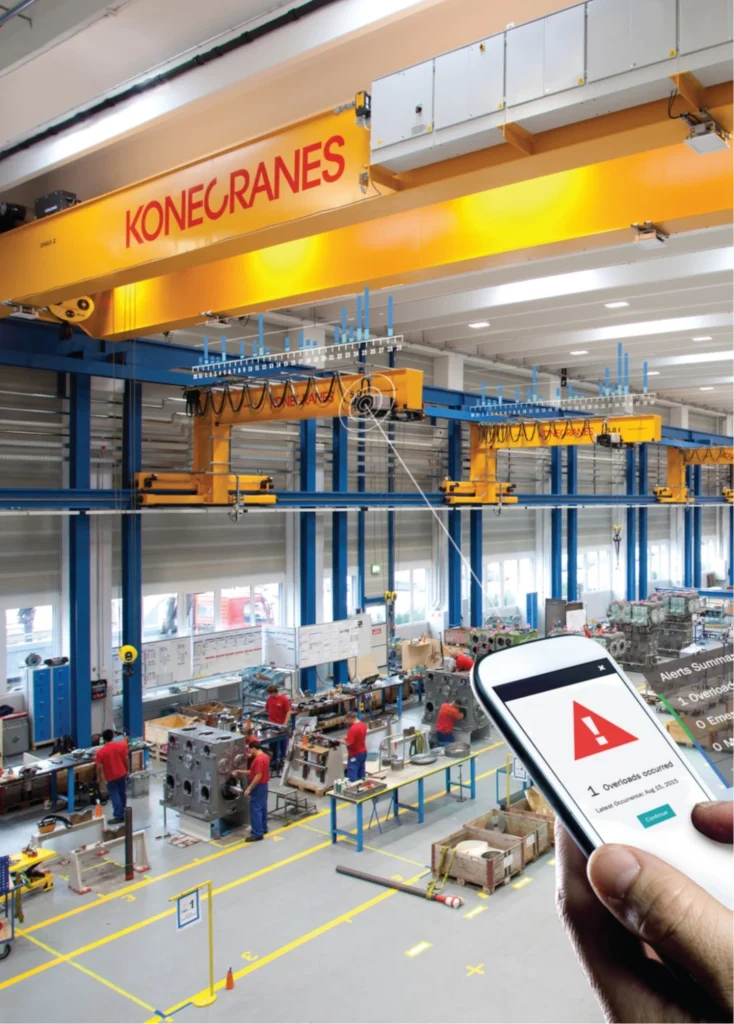
One feature that I would like to highlight of the SIMOCRANE CMS, which makes it unique and especially useful, is the Replay Function. SIMOCRANE CMS Replay Function is a tool that enhances operational efficiency and safety by recording and replaying crane operational data. This feature provides operators and maintenance teams with a clear visualisation of crane activities, including load movements, environmental conditions, and operator commands during specific periods. By enabling the review of past crane operations, it aids in root cause analysis of incidents or performance bottlenecks, facilitates training, and supports ongoing process optimisation. You’re basically able to go back in time and review exactly what occurred to track down and correct intermittent issues, which a lot of maintenance personnel appreciate.
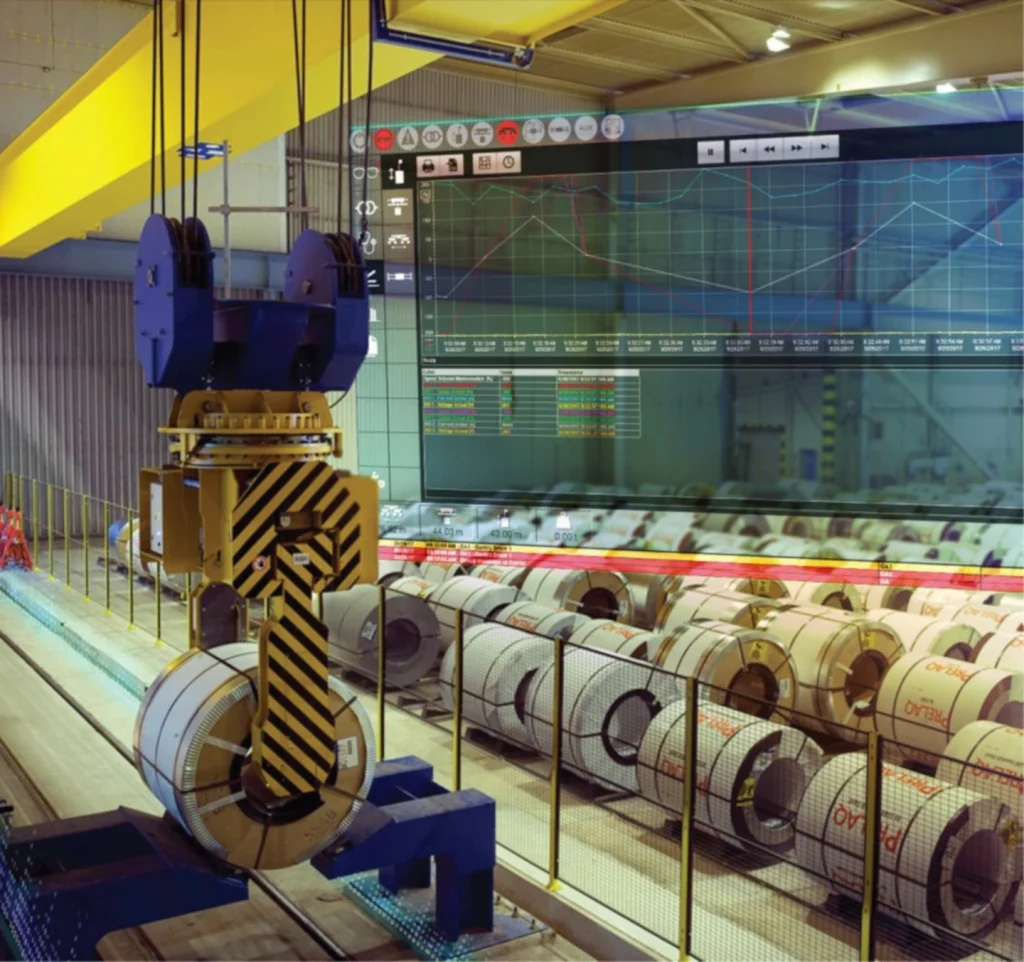
Joan Hexter-Christensen, Vice President, Business Line Field Service, Konecranes: Konecranes has consistently been at the forefront of crane technology, making substantial investments to integrate advanced features into both large process cranes and standard cranes utilised across various sectors. Our dedication to innovation ensures that even standard cranes are equipped with state-of-the-art technologies, thereby enhancing safety, precision and efficiency in lifting operations. The Konecranes X-series exemplifies this commitment, offering high-tech solutions that were previously exclusive to more complex systems. This series includes advanced features such as stepless control and Smart Features like Hook Centering and Sway Control, which significantly improve the safety and precision of lifting operations. The integrated radio control with a display and the crane’s smart, connected components facilitate intuitive and efficient operation, allowing for real-time updates and over-the-air upgrades without the need for hardware changes.
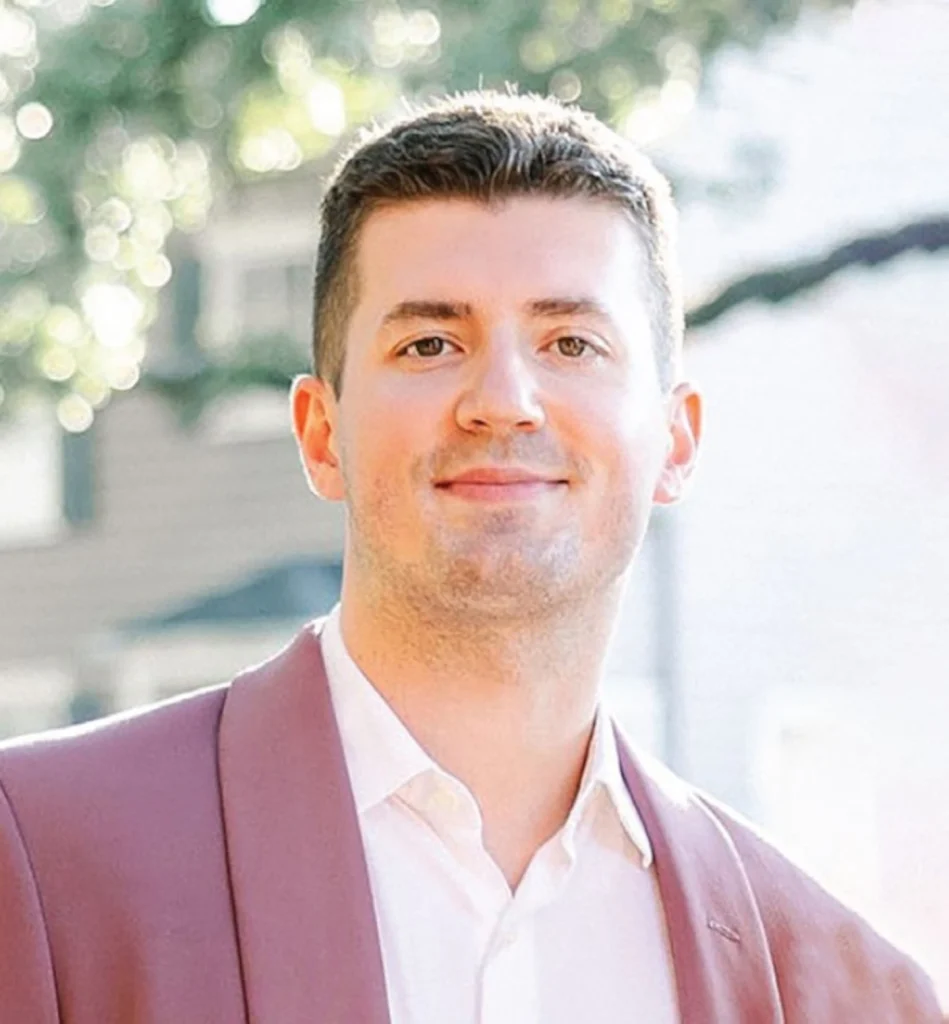
Moreover, Konecranes provides a suite of digital services to support an advanced, data-driven approach to equipment and maintenance. Core of Lifting technologies power an array of Konecranes Smart Features, while TRUCONNECT, our real-time equipment monitoring system, offers online web access through the Konecranes Customer Portal. Additionally, Konecranes’ Lifecycle Services deliver data-based maintenance insights as part of our comprehensive service delivery. From online storefronts to custom APIs, and from real-time alerts to full automation, Konecranes offers a wide range of customisable, digitally enabled services to meet our customers’ needs and ensure optimal performance of lifting equipment.
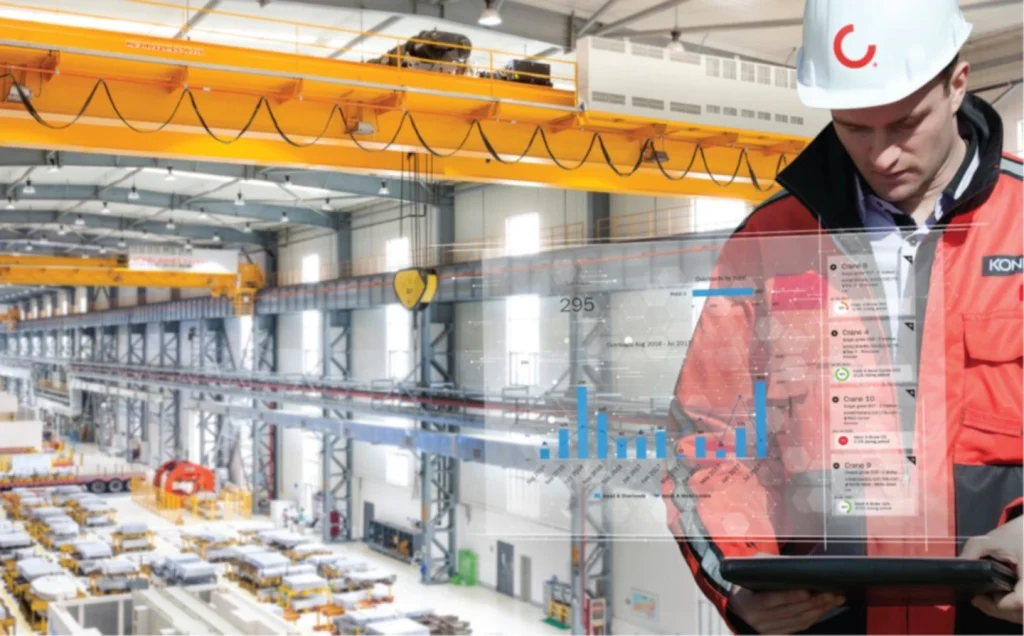
OCH: Industrial automation has seen a dramatic rise over the past five years. Are there any areas or improvements to the components/technology that you think can be added in the future to improve safety and efficiency?
RN: I think the performance of such a system is based on a couple of factors: the data that is fed into it and what is done with that data. Although the market has widely implemented the use of crane-mounted sensors, wearable technology (such as AR-integrated wearables and RFID trackers) for operators and other personnel is not as common. There is room for improvement in the technology, implementation and integration of wearable sensor technology when it comes to industrial automation. In addition to increased use of wearable technology, implementing AI and machine learning (ML) to analyse the data coming from all of these sensors in real time can predict and prevent breakdowns, improve KPIs and eliminate safety risks. I think AI and machine learning can be particularly useful for analysing video feeds for real-time hazard detection and behavioural analytics. So, to improve safety and efficiency, we must improve the data being collected, as well as improving what should be done with the data, which can be accomplished by increased use of wearable technology and AI/ML.
JHC: One of the most promising areas for enhancing industrial automation lies in integrating technology with the daily operations of factory workers and crane operators to improve safety and efficiency. By focusing on how operators interact with equipment, rather than solely on the physical equipment itself, we can develop solutions that are not only innovative but also practical and user-friendly. For example, implementing intuitive control systems and realtime feedback mechanisms can help operators make more informed decisions, reducing the likelihood of accidents and equipment failures.
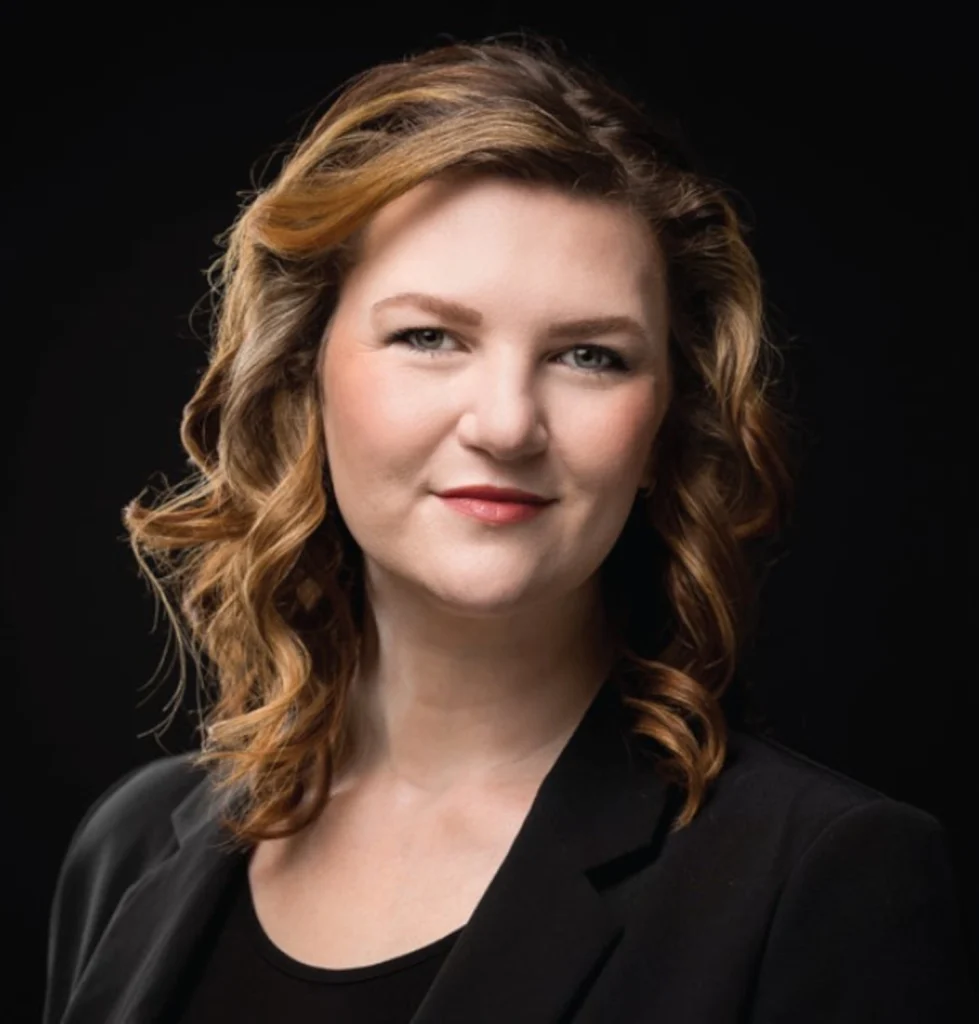
OCH: In addition to the standard intelligence you provide, do you receive any unique requests for further analysis from your clients? If so, can you elaborate?
RN: Yes, there was feedback that was provided by one of our customers, which we incorporated into our solution because it was such a great recommendation. That recommendation was to incorporate camera feeds into the data collection system. Typically, our CMS system collects and stores data from various devices such as VFDs and other field sensors, which aids maintenance in troubleshooting a system, and getting it back into operation. Although the CMS system could help them get the system back into operation, the cause of the issue was unexplainable. After adding cameras, they identified operator errors that were causing the issues. Having all of the data alongside visual video feeds painted the full picture.
JHC: Konecranes is dedicated to offering customer-specific advice at all times, tailored to meet the unique needs of each client. This includes, for example, remote support requests, individual equipment performance evaluations, anomaly analysis, and assistance with equipment upgrades and process optimisation.
OCH: What are the most frequent challenges that clients present to you and what solutions do you provide to overcome them?
RN: Most of the applications that clients present to us are existing systems, which consist of various OEMs and vendors, and complex integration.
In this case, your options are to implement a flexible solution that works with what they have, or you have to replace a majority of the controls (VFDs and PLCs), which can lead to a costly and time-intensive investment. This is the exact reason that SIMOCRANE CMS was built upon the idea of flexibility. In this instance we’re able to offer a solution that will work with their existing controls and sensors, and give them an option on whether they want a local or centralised approach, which covers almost any requirement we’ve come across. Another challenge that we face quite often is providing a solution that works with their existing (often dated) infrastructure, which is more prevalent when considering a centralised solution, because the cranes have to be connected to a central server for the data to be analysed. Finding WLAN frequency bands and channels that are free, signal interference and integrity and other environmental factors all contribute to a challenging scenario. To overcome these challenges we utilise our SCALANCE team to perform a wireless site survey, who then recommend the most reliable and cyber-secure solution to collect data off of the cranes.
JHC: As a broad-brush statement, the most frequent challenges customers are presenting in regards to performance monitoring overhead lifting equipment is really about equipment optimisation. Given the dynamic nature of the industrial world, how can we support a prescriptive service experience to ensure uptime, while minimising costs? Solving this problem looks different for each customer and varies depending on the customer’s needs. The mix of regulatory compliance, OEM requirements, environment and usage are all factored in designing a CARE Preventive/Predictive Maintenance programme with Konecranes Field Service. We offer a range of solutions, from advanced consultation services supporting equipment and performance evaluations, through to electrical and digital retrofit services, all designed to support the service experience right fit for our customers’ needs and appropriate within their digital journey.
OCH: How do you think technology will continue to evolve in the future and how will this impact the future of the industry?
RN: With the direction that the industry is heading, I believe the major components of the technology that will evolve will be: AI/ML for data analytics (from various data sources including VFDs, sensors and video), increased integration of cobots (collaborative robotics), industrial AR (augmented reality), remote control operation stations, and digital twins. More data is being collected than ever before, thus the analytics behind the data must also evolve to turn it into useful information – for example, identifying dangerous situations and safely stopping a machine before an accident occurs. Or predicting when a machine needs maintenance based on vibration/temperature sensors to prevent downtime and potentially unsafe situations. AI/ML is a natural fit to solve these challenges.
Increased integration of cobots is yet another reason to implement a flexible and modular system. Some of the advanced cranes out there are basically giant robots, but these cranes not only have tasks to perform, they also have to integrate with other machines such as transfer cars, shipping bays, etc. The easier it is to integrate these machines together, the more fluid an industrial process becomes. Naturally, I believe systems from various vendors will move toward becoming more easy to integrate.
AR in industrial settings can include wearable devices like AR lens, which can provide spatial awareness and provide augmented reality overlays, which can aid in tasks like equipment diagnostics. Staffing and training personnel is a pain point a lot of facilities are experiencing and AR can decrease the amount of time required for training new employees and even improve the performance of long-time employees.
I believe that removing operators from dangerous environments and moving them to a safe and comfortable location where they can control a crane remotely will become more commonplace. The SIMOCRANE Remote Control Operation System (RCOS) by Siemens is a cutting-edge solution designed to enhance crane operation through remote control, emphasising safety, productivity and operator comfort. It enables operators to manage cranes from a remote office environment, maintaining productivity levels comparable to traditional cabin-controlled systems or even exceeding them. The ‘any-to-any’ function allows an operator to control any connected crane from any connected remote desk. For example, if you have a facility that has semi-automated cranes, you can have one operator controlling multiple cranes, which would only require occasional operator intervention, reducing resource requirements.
Finally, I believe digital twins will be the future. A digital twin is a virtual representation of a physical product, process or plant that integrates real-world data to simulate, test and optimise performance throughout the life cycle of a system. The digital twin bridges the gap between the physical and digital worlds by using simulation, real-time feedback and predictive analytics to enhance design, production and operations. Digital twins provide actionable insights through detailed data analysis, helping industries address complexity and variability effectively. Companies can design and simulate products or systems virtually before committing to physical prototypes, reducing development time and costs while improving accuracy and reliability. Simulating and refining manufacturing processes in the virtual realm speeds up the time-to-market for new products.
By embracing these technological advancements, industries can unlock unprecedented levels of safety, efficiency and innovation, positioning themselves to meet future challenges and opportunities with greater agility and resilience
JHC: The industrial digital transformation is well underway but lagging behind the broader consumer market. As new equipment comes online, there is a potential for customers to proactively design a connected, integrated, equipment infrastructure to really build an on-demand service experience. Yet, while technology is here to stay, equipment regulations are presently unchanged, and the world is evolving in how we consider, regulate and use data. I expect us to continue to exploit data in every way possible to continue to pursue equipment and business result optimisation. However, magic lies in unlocking potential between mixed technology architecture, ageing non-connected equipment, varied infrastructure, changes in workforce, and balancing costs.