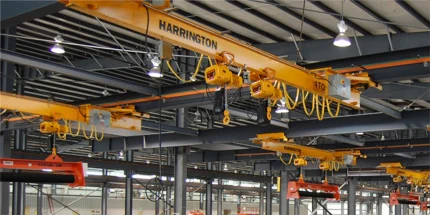
In addition to these five steps, HMI offers a complimentary publication: “Recommended Practices for Electric and Air Powered Hoists.” The free document includes a comprehensive collection of “shalls” and “shall nots” to create the safest operating environment.
Step # 1: Check Powered Hoist Motion
In this step, the operator verifies that the powered hoist moves in the same direction indicated by the buttons on the controller. Weber advised pushing the up button first.
“If pushing that up button results in the raising of the hook, then it’s okay to proceed with checking the lowering function,” he said. “If it ends up lowering, it’s crucial to lock out and tag out that hoist immediately as this is indicative of a phase reversal.”
Weber said that hoist owners and operators frequently — and mistakenly — interpret this reversal as occurring in the wiring of the controller. While that is possible, it’s also equally likely the issue is at the hoist itself, at the power supply, or at the crane connection
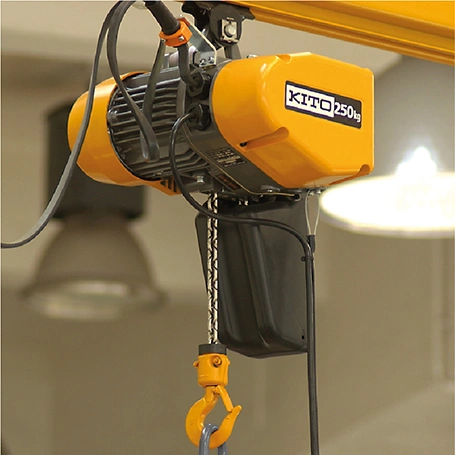
“The worst mistake to make in this case is misidentifying the cause of the reversal and rewiring the controller buttons,” continued Weber. “Also, a phase reversal can occur both on existing and new equipment at any time if someone is working on the system. That’s why it’s important to perform this test at the beginning of every shift.”
A phase reversal is not only dangerous in that the powered hoist does not move as expected, but also because it may result in a two-block condition. A two-block occurs when the hoist load block raises to the point of contacting the hoist body, he said. “This can cause damage to parts of the hoist, or worse — cause the load to drop.”
Step # 2: Verify Over Travel Limit Switches Work Properly
Before applying the load, the operator should also confirm that the hoisting over travel limit switches function properly. These electro-mechanical devices stop a lifting movement at a certain point to prevent an accident. If all hoist users follow the manufacturer’s operating instructions, they won’t use over travel limit switches as routine operating stops. Doing so can cause the switches to fail.
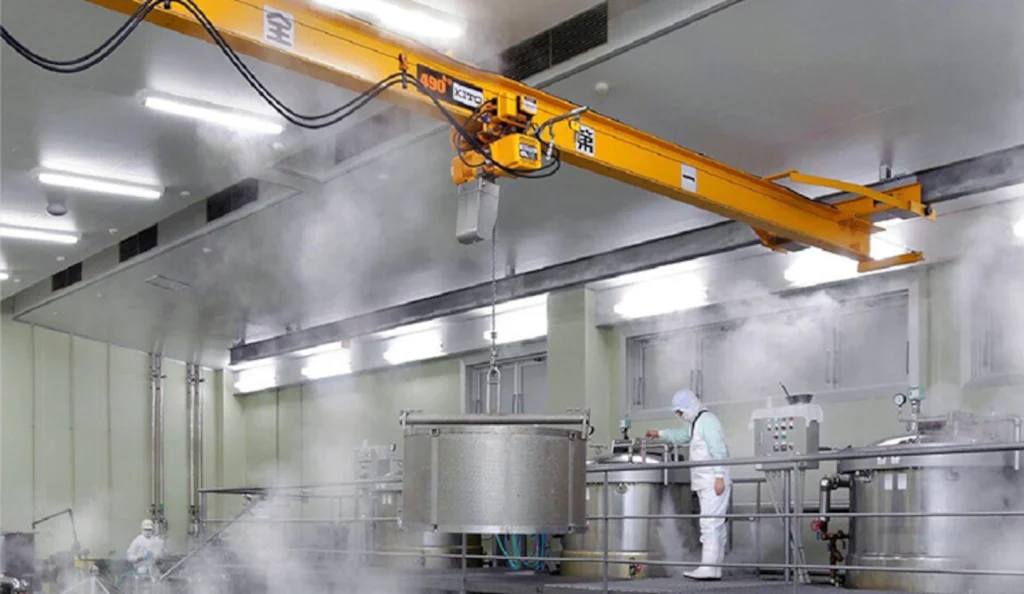
“After checking the lift and lower functions, the operator should raise the hook to the upper limit switch,” Weber said. “This confirms that the switch stops the up motion. If a lower hook limit switch exists, the operator should also ensure that that lower limit switch is operational.”
An exception to this practice, he added, is when using slip clutch hoists. “Do not test that lower limit switch or stopping for a slip clutch hoist. If that limit switch is not there, that could cause damage to the clutch mechanism,” said Weber.
Additionally, if a crane trolley travel limit switch is present, the operator should verify its proper operation in both directions prior to using the hoist.
Step # 3: Inspect Rope or Chain for Damage
Next, the hoist operator should closely examine the hoisting wire rope or chain. Signs of chain wear include nicks, gouges, dents, or deformation. Wire rope damage could include kinking, distortion, unstranding, deposits, corrosion, or birdcaging (when the strands surrounding the core are separating from it).
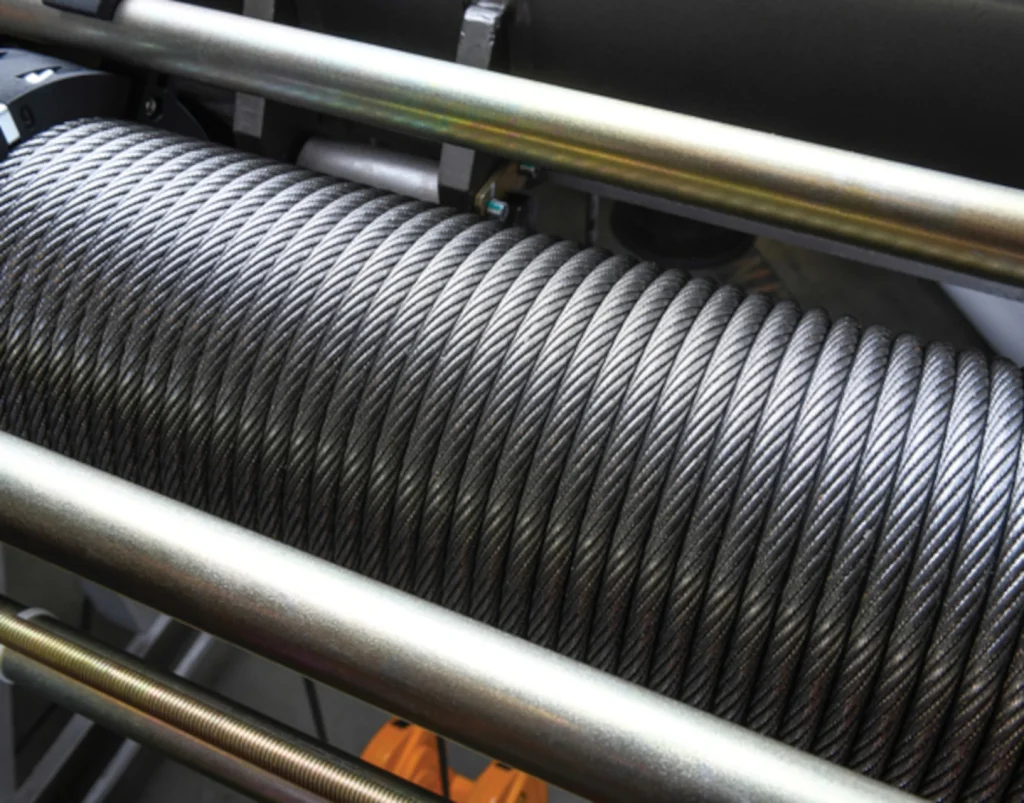
“Birdcaging is a sign that shock loading has happened,” Weber explained. Shock loading occurs when the operator lifts or releases the load suddenly. “Additionally, check to make sure that the wire ropes are properly seated in the drum grooves and sheaves prior to operation.”
Upon discovering wire rope or chain damage, do not permit the operator to use the hoist. Instead, the operator should report the issue to a supervisor and the hoist locked out/tagged out until it repairs are complete.
Step # 4: Confirm Load is Centered Under the Hook
Side pulling a hoist is unsafe for multiple reasons. It can lead to the load swinging out of control and possibly striking the operator or other personnel. A swinging load could also impact structures or equipment in the facility, as well as damage the hoist and the trolley.
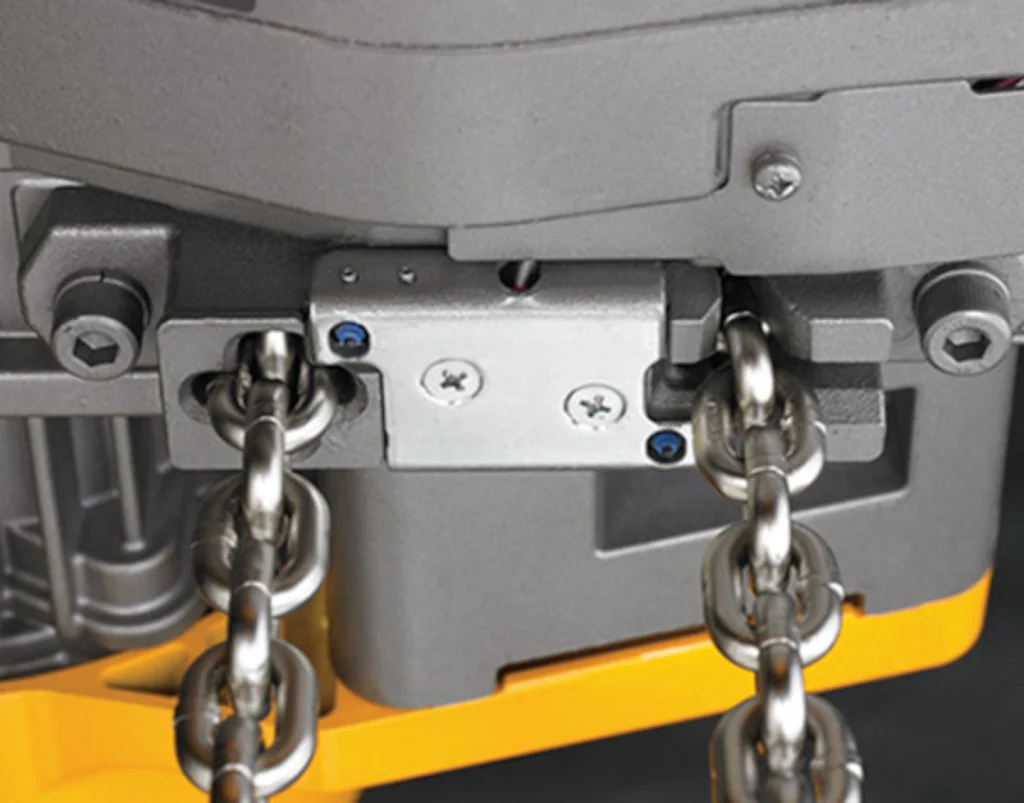
“Don’t operate the hoist unless the load is centered under the hook,” cautioned Weber. “If the wire rope is unable to form a straight line from the suspension of the hook, it can pull the ropes out of the drum grooves.”
Further, side pulling a hoist puts significant stress on the equipment and its components. This will cause premature wear and shorten the lifespan of the equipment.