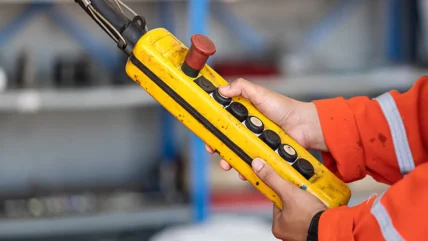
Why Pre-Shift Hoist Inspections Are Important
Pre-shift hoist inspections are important because hoists lift and lower heavy loads overhead. A hoist failure could potentially lead to the load falling from its suspended height, endangering the lives of personnel. A drop could also damage the lifted product, surrounding equipment, and facility structures.
Additionally, routinely verifying that a hoist is in safe, proper operating condition maximizes productivity. This confirmation reduces the risk of unplanned downtime and can extend the service life of the hoist.
Codes and Standards Call for Inspections
Multiple safety regulations and standards call for performing pre-shift hoist inspections. Sources include the Occupational Safety and Health Administration (OSHA), the American Society of Mechanical Engineers (ASME), and HMI. Applicable codes and standards are:
- OSHA-CFR 29 Part 1910.179 for overhead and gantry cranes (to which hoists attach) requires inspections of new and modified cranes and hoists. This federal regulation calls for a trained, qualified professional to perform inspections prior to use and at regular intervals.
- ASME B30.16 Overhead Hoists (Underhung) mandates that qualified, trained persons conduct regular inspections of powered underhung overhead hoists.
- ASME B30.21 Lever Hoists calls for regular inspections of manually powered lever hoists performed by qualified persons trained to do so.
- ASME B30.10 Hooks covers the visual inspection of hooks and slings used with hoists.
- HMI 100.24: Inspection and Maintenance Manual – Hoist provides information and suggestions for the inspection of overhead hoists.
- HMI 100.74: Inspection and Maintenance Manual – Lever Hoist offers recommendations and best practices for the inspection of manually-operated lever hoists.
What to Look for During Pre-Shift Hoist Inspections
There are several key areas to assess when performing a pre-shift hoist inspection, noted Matthew Frazier, Senior Manager of Engineering in New Product Development at HMI member Columbus McKinnon. Frazier presented this portion of the webinar.
- Is an out-of-order or out-of-service tag attached to the hoist?
- Are the warning labels on the hoist present and intact?
- Do all motions properly match control device marks?
- Are the hook and latch working properly or are they damaged or deformed?
- Is the wire rope broken, kinked, or improperly wound?
- Is the load chain not worn, stretched, twisted, or distorted?
- Do the travel limits and hoist limit switches function properly?
- Are there any abrasions, wear, or weld splatters on the hoist that could inhibit its operation?
- Does the hoist make any unusual sounds in operation?
- Are there any obstructions in the surrounding area or travel path of either the operator or the hoist that could pose a hazard?
“The pre-shift hoist inspection should also include any guidelines or areas for assessment recommended by the hoist’s manufacturer,” Frazier added. “Those are in the equipment owner’s manual.”
Also, the operator should document the findings of every pre-shift hoist inspection, either on paper or electronically. The facility should retain those records to confirm they are being performed and to identify any areas of concern or patterns of wear.
“For operations needing more help with establishing a pre-shift hoist inspection process, HMI offers a comprehensive guide. HMI 100.24 Hoist Inspection and Maintenance Manual is a free download,” said Frazier. “The manual also includes helpful checklists that detail these key inspection areas.”