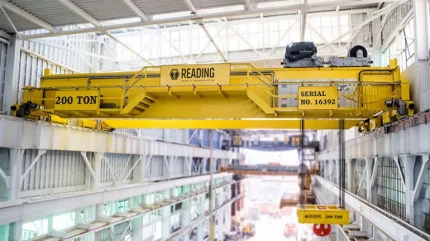
The Dangers of Off-Center Picks
Attempting to lift a load that is not directly beneath the hoist can cause it to swing when the operator raises it. This off-center pick situation creates several dangers, including:
- Potential injury to personnel as if the load swings out of control, striking the operator other workers nearby.
- Possible damage to the facility or equipment should the swinging load strike structures or machinery.
- Damage to the hoist due to the excessive stress an off-center pick causes. Using a hoist to lift an off-center load strains components. This includes the hook, chain or wire rope, load block, pocket wheel, reeving, or gears. The stress leads to premature wear, shorter service life, and greater risk of failure.
- Damage to the trolley, as the off-center pick’s forces cause it to tip to one side or the other of the bridge beam. Designed to support weight evenly across its wheels, a side-pulled trolley will experience premature wear and deformation of the unit. An extreme off-center pick can potentially pull the trolley off the beam.
- Cumulative damage to the overhead lifting system from off-center picks can lead to catastrophic failure of the hoist and trolley.
Detection System Prevents Off-Center Picks
There are a variety of smart overhead lifting technologies that intuitively predict a problem in real-time and alert the operator. Among these solutions are off-center pick detection systems.
Off-center pick detection technologies utilize with sensors. These devices may use angle sensors to detect the angle of the rope. Alternately, some incorporate vision sensors that determine the misalignment of the load relative to location of the rope or chain at the hoist drum. When the sensor identifies an off-center pick, a visual indicator light or audible alarm on the controller alerts the operator of the unsafe situation.
To further boost safety, a facility owner can elect to enhance an off-center pick detection system with the addition of other technologies. Some systems prevent the off-center lift from occurring. Others automatically center the bridge and trolley over the load to ensure proper alignment and prevent the side-pull.
Improve Overhead Crane Safety and Productivity with Other Technologies
In addition to off-center pick detection systems, there are multiple other optional features available to enhance both safety and productivity in overhead lifting.
An Overhead Alliance webinar details a variety of smart crane technologies — such as those that minimize load sway, detect load snags, alert operators to potential collisions, and more. The “Overhead Lifting Safety Innovations Panel Discussion” helps overhead crane and hoist operators, maintenance personnel, owners, safety professionals, purchasers, and specifiers explore some of these solutions. It also covers approaches that address the safety and productivity challenges associated with overhead lifting.
Meet the Overhead Alliance
MHI’s Overhead Alliance includes the Crane Manufacturers Association of America (CMAA), the Hoist Manufacturers Institute (HMI), and the Monorail Manufacturers Association (MMA). All three industry groups are a part of the Occupational Safety and Health Administration’s (OSHA) Crane, Hoist and Monorail (CHM) Alliance. Through this collaboration, the organizations provide information, guidance, and access to training resources. These tools help protect the health and safety of worker using hoists, cranes, and monorails. For more information, visit mhi.org/solutions/overhead-alliance.